Project Background:
Zhuhai Gree Electric Appliances Co., Ltd. is China’s leading electrical appliance manufacturer and a leading enterprise in China’s manufacturing industry. Founded in 1991, it is an international home appliance enterprise integrating R&D, production, sales and service. It has three major brands: Gree, TOSOT and Jinghong. Refrigerator and other products.
Before the introduction of the equipment management system, Gree’s equipment management method was to manually follow up and maintain various information status of the equipment, manually log in to the account, and the management method was backward. There was no effective data collection for the entire life cycle of the equipment, and data was not shared among the various units of the group. This leads to difficulties in resource allocation and standardized group management. Mainly as follows:
1. Business process management is complex:
The purchase and management of equipment are manually maintained and registered. In particular, the purchase part adopts the centralized purchase of the group. The management process is complicated, and real-time dynamic feedback cannot be performed, and the process is solidified.
2. The management system and management methods are backward:
The equipment management business model of each branch of the company is inconsistent, and they are all “separate”, so the management system is inconsistent, which is not convenient for unified management at the enterprise level.
3. The islanding of information communication:
Because the comprehensive information query of basic data is not intelligent, the centralized application, approval, procurement, acceptance, use and maintenance status data of equipment cannot be collected and displayed on the same platform, resulting in the phenomenon of “information islands” among various departments , each business department cannot obtain the data in the life cycle of the equipment to which it belongs, and has no clear understanding of the overall status of the equipment. Moreover, the company currently does not have a platform to centrally manage the equipment information of various subsidiaries and branches, and the equipment information cannot be shared.
In 2018, the group introduced the SAMEX equipment management system to realize the whole life cycle management of the group equipment.
System design blueprint:
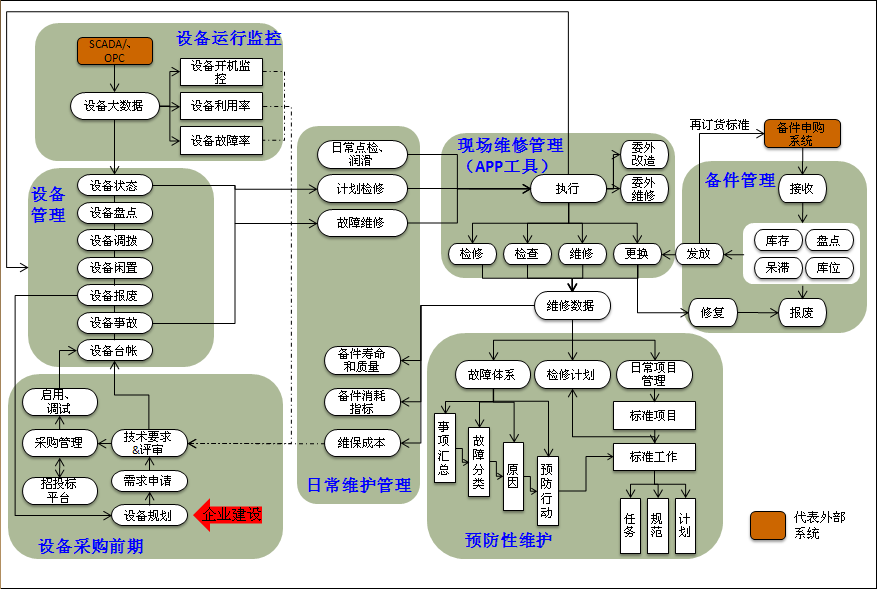
Gree currently has more than 70 subsidiaries and branches using the SAMEX system: including Wuhan, Chongqing, Hefei, Changsha, Zhengzhou, etc.
The main modules implemented by the entire group include: equipment purchase management, equipment procurement management, supplier bidding management, equipment acceptance management, equipment account management, spare parts management, work order management, tooling tool management, and fixed asset management.
Implementation module:
(1) Subscription management
1. Process reengineering, optimize the approval process (parallel approval), and improve the quality and efficiency of order processing;
2. The equipment introduces the material coding management method to realize the standardization of the group equipment coding;
3. Standardization of equipment technical requirements;
4. Equipment technical bid evaluation realizes online bid evaluation:
Specialization of bid evaluation: the first online bid evaluation model for technical bid evaluation, and the establishment of an expert model for bid evaluation by each unit to improve the professionalism of technical bid evaluation results
Standardization of bid documents: standardize the content of suppliers’ bid proposals, improve bid quality and bid evaluation efficiency
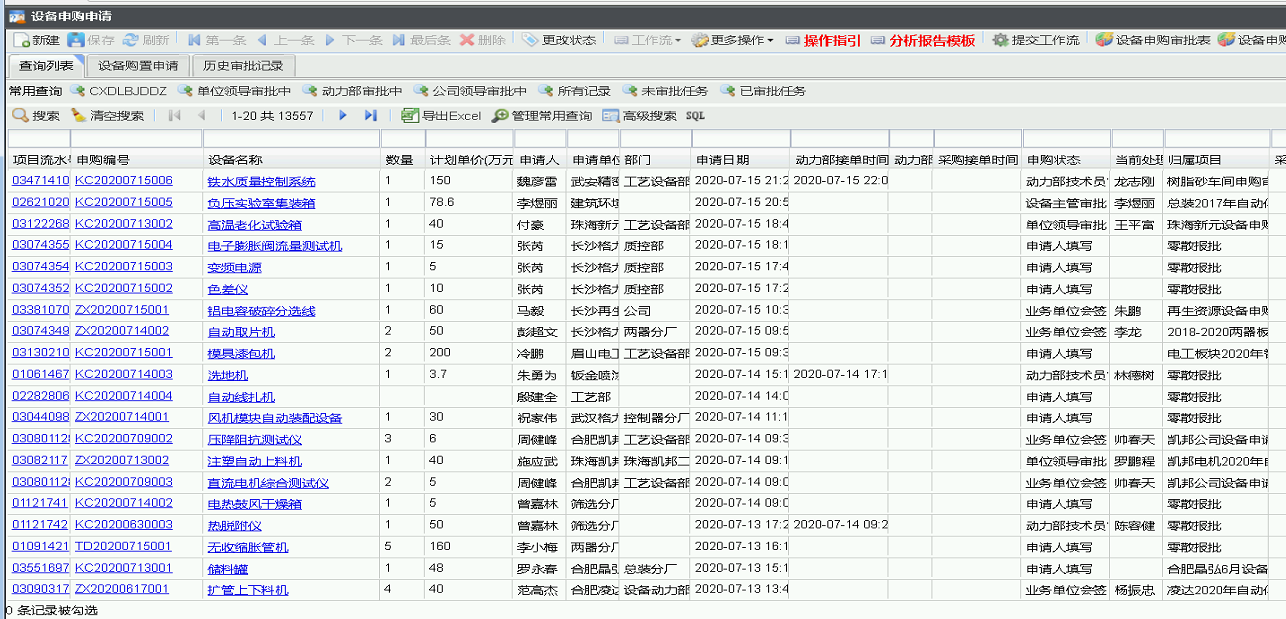
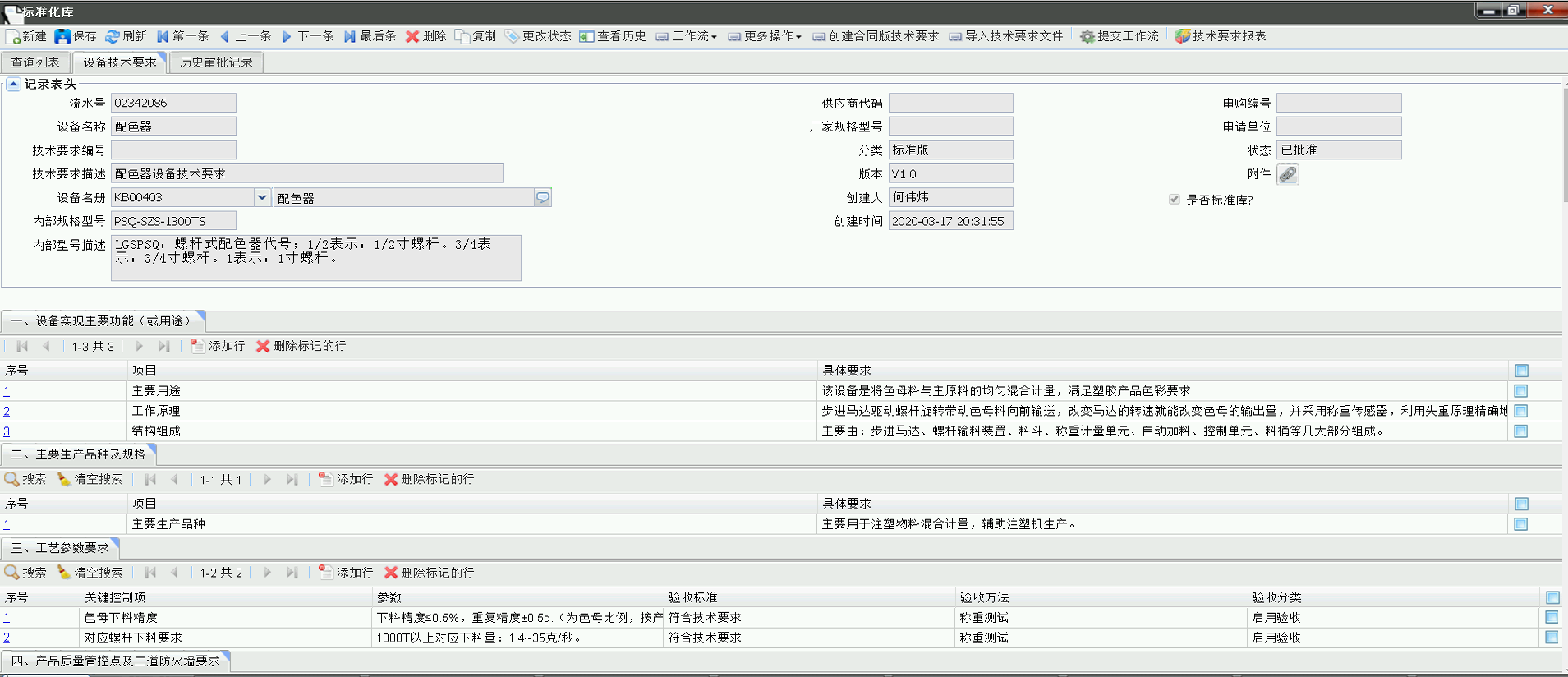
Technical evaluation form:
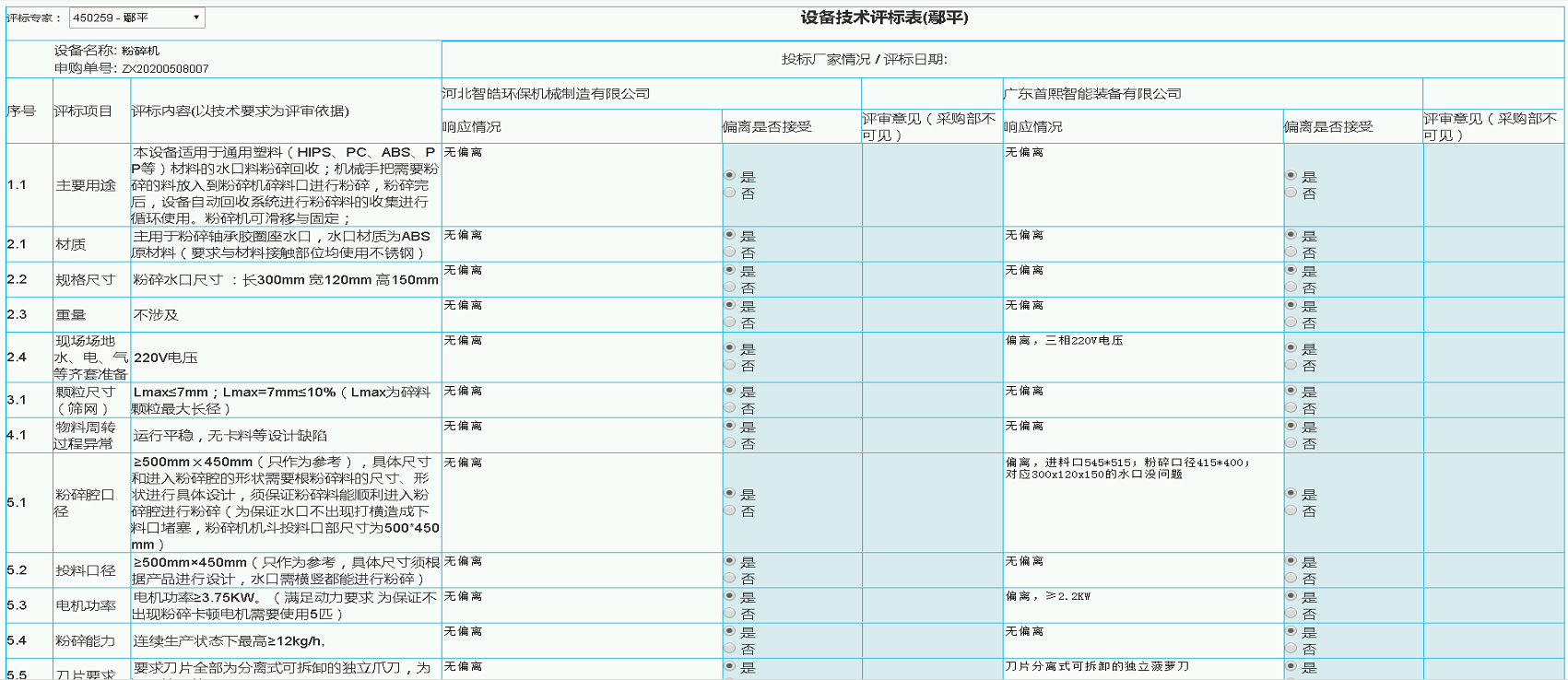
(2) Procurement management
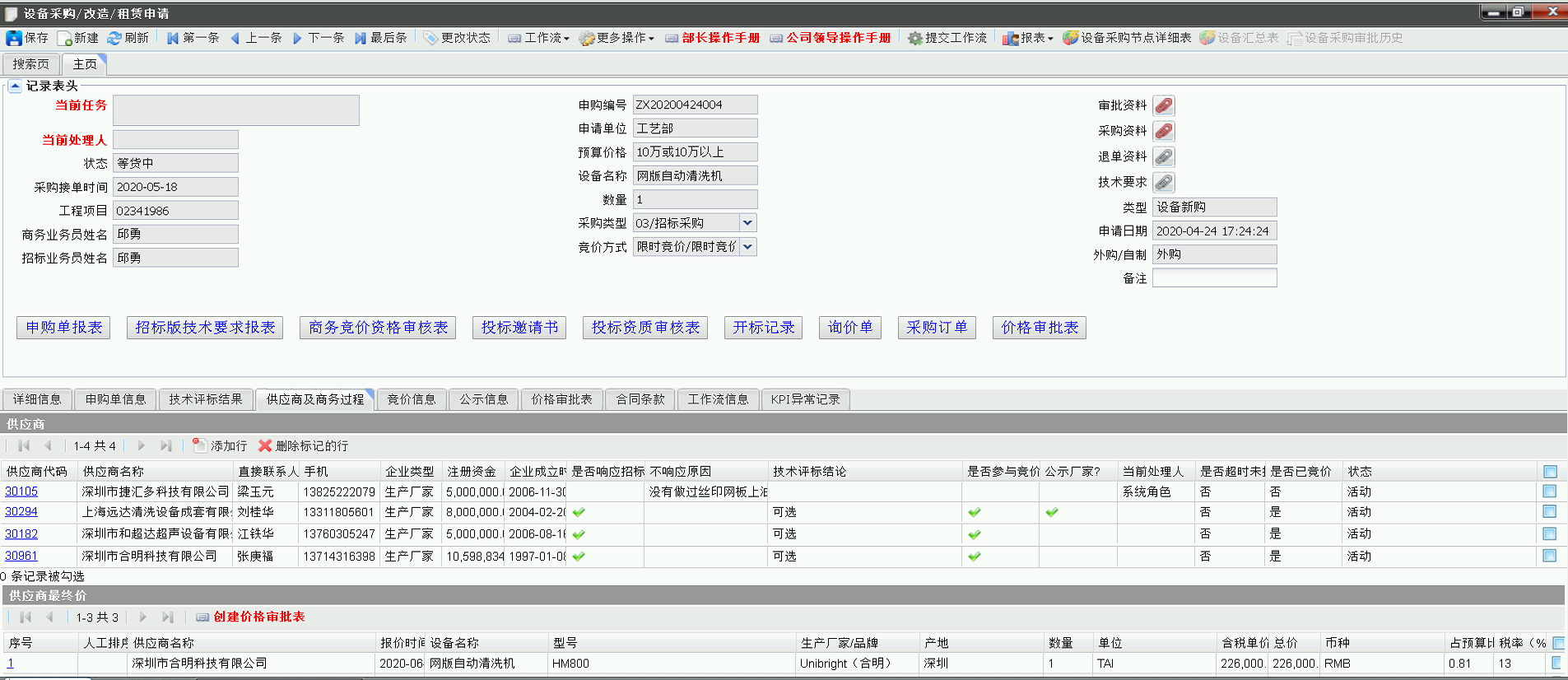
(3) Supplier and bidding management
Suppliers conduct supplier information registration, online bidding, quotation, and bidding through the bidding platform. It realizes the informationization of equipment procurement bidding, optimizes the monitoring and speed of the procurement bidding process, and makes the bidding process transparent and traceable.
Supplier basic information:
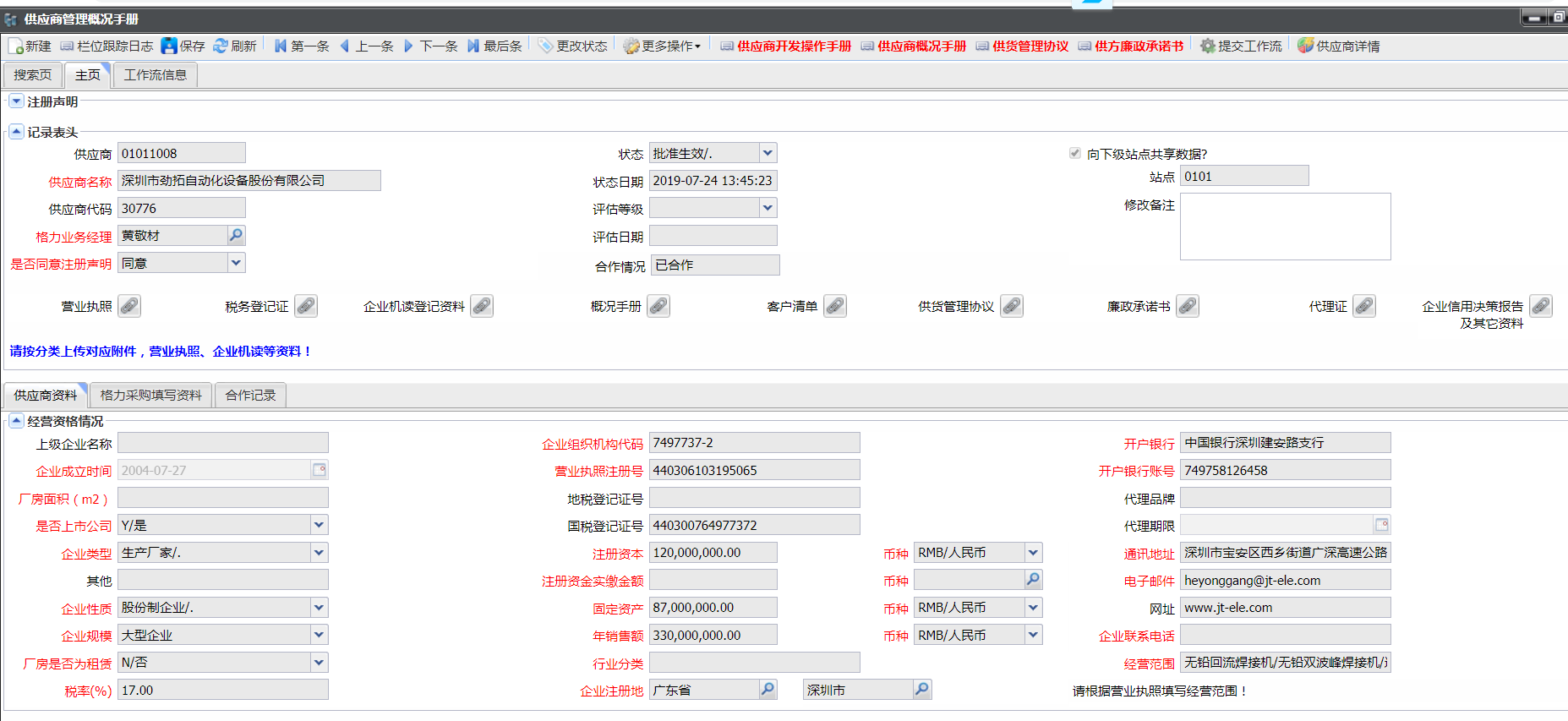
Supplier bidding interface:
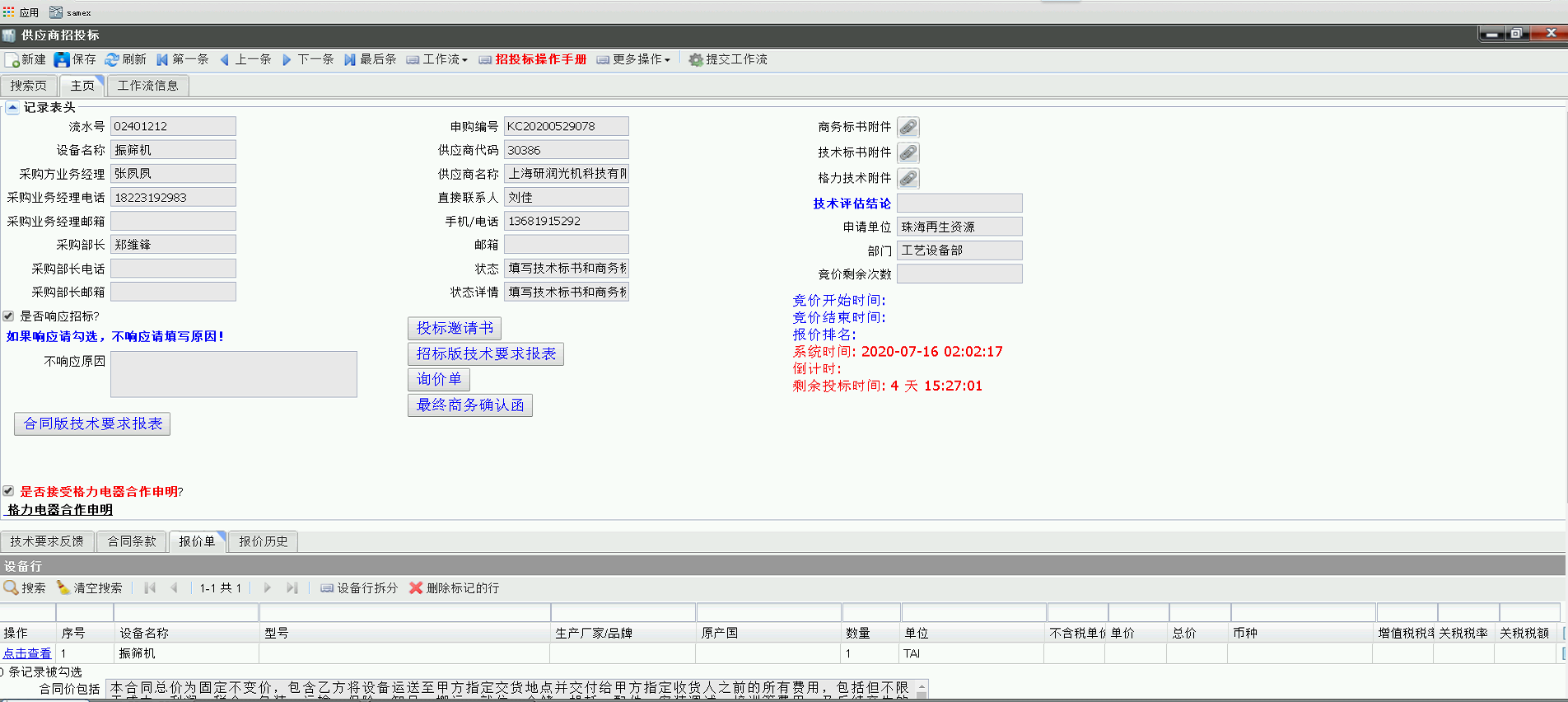
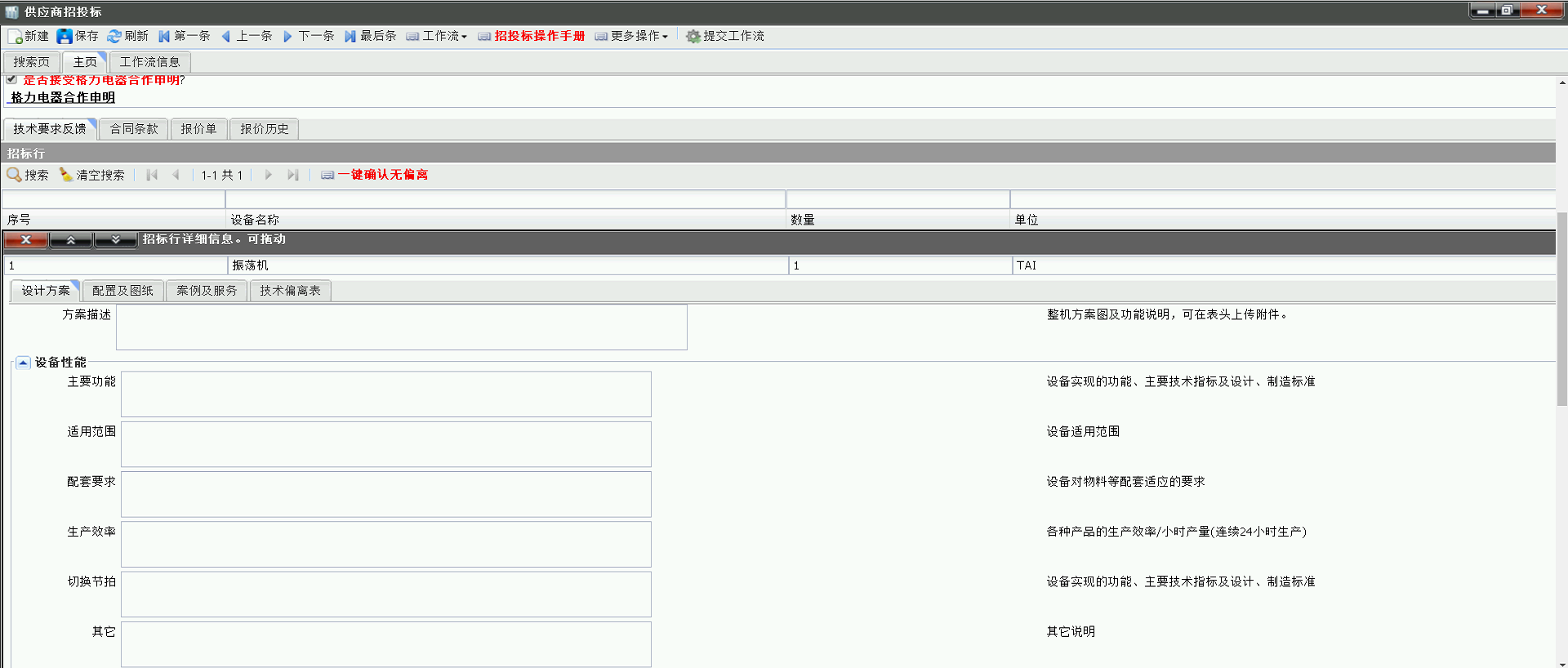
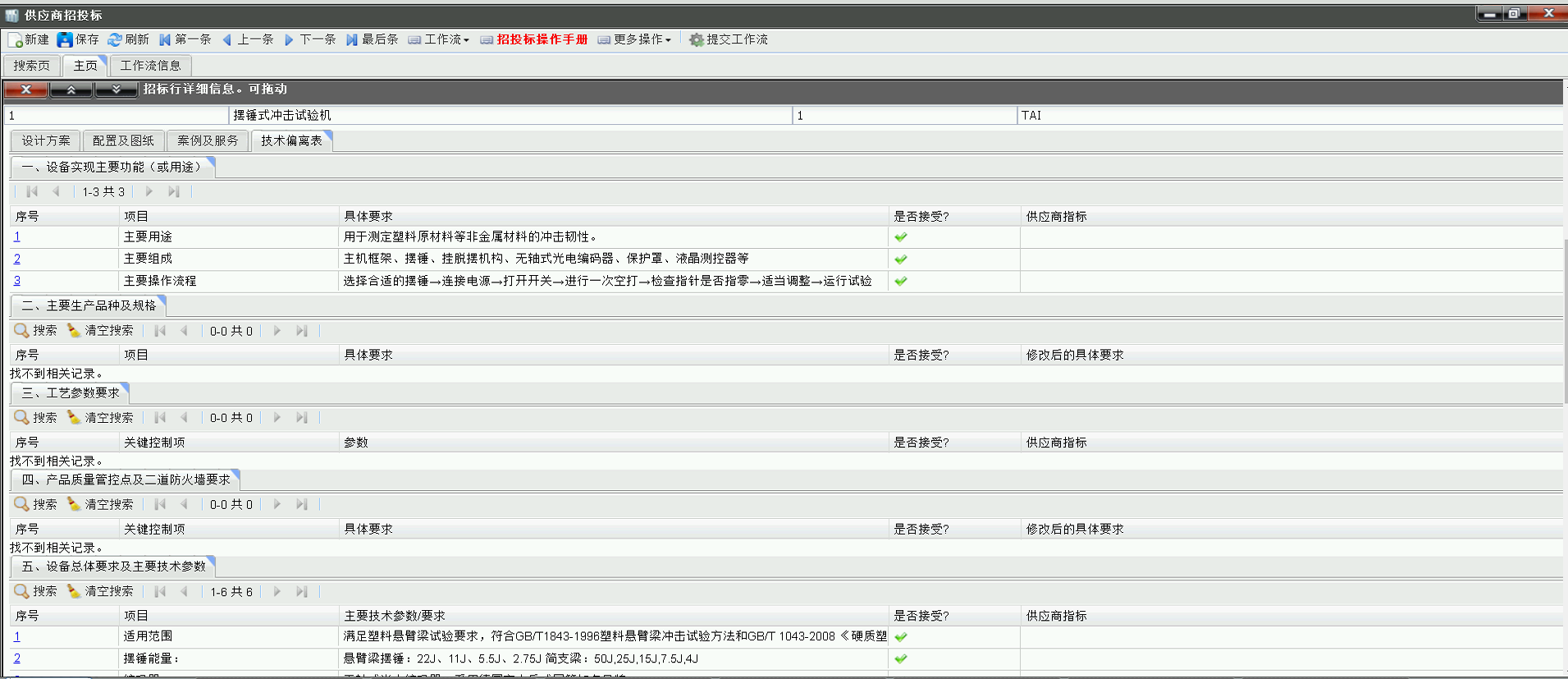
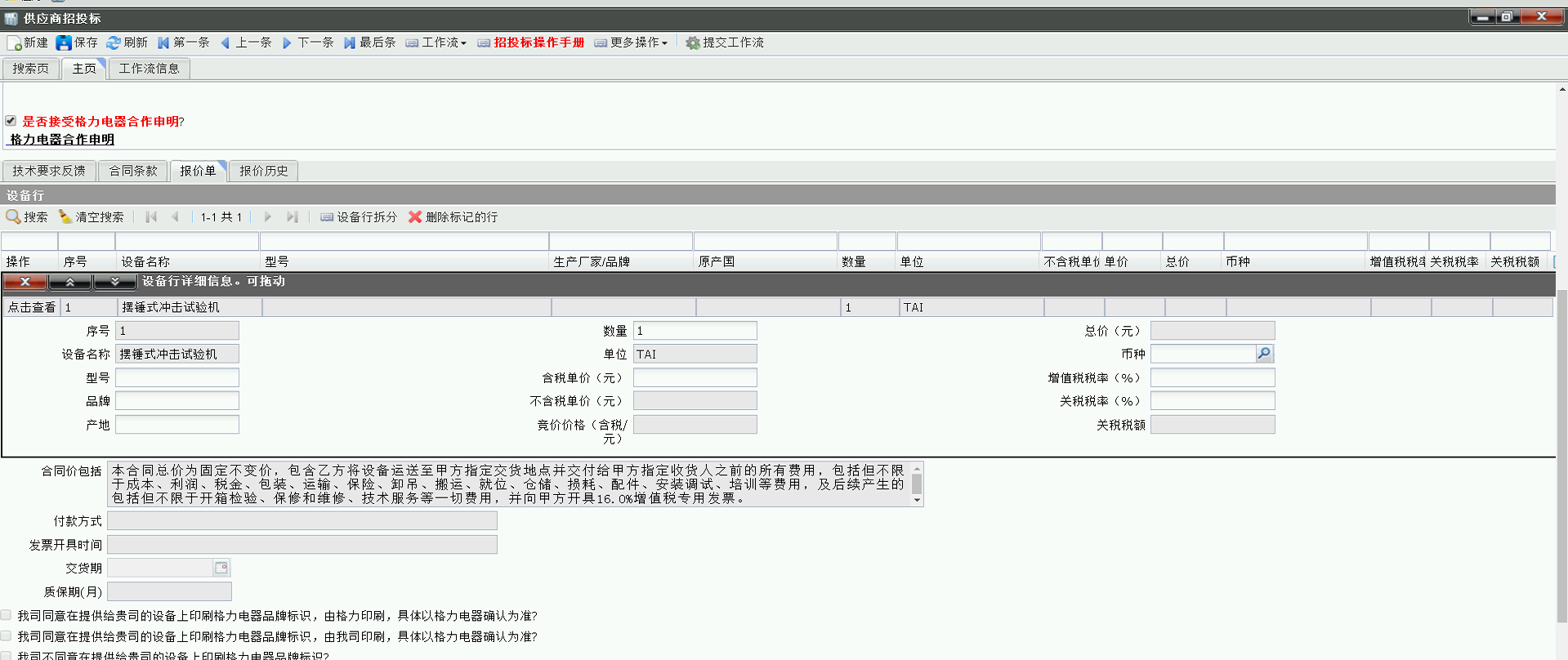
(4) Equipment acceptance closed-loop management
Pre-acceptance, unpacking, start-up, and final acceptance are closely linked, and the process records are archived completely.
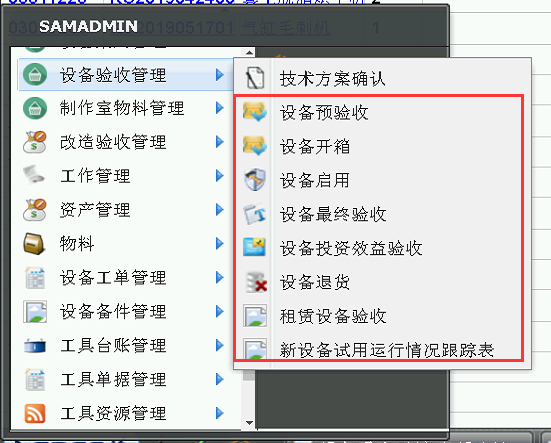
(5) Equipment ledger management
At present, the number of asset ledgers managed by the entire group in the system is about 85,000.
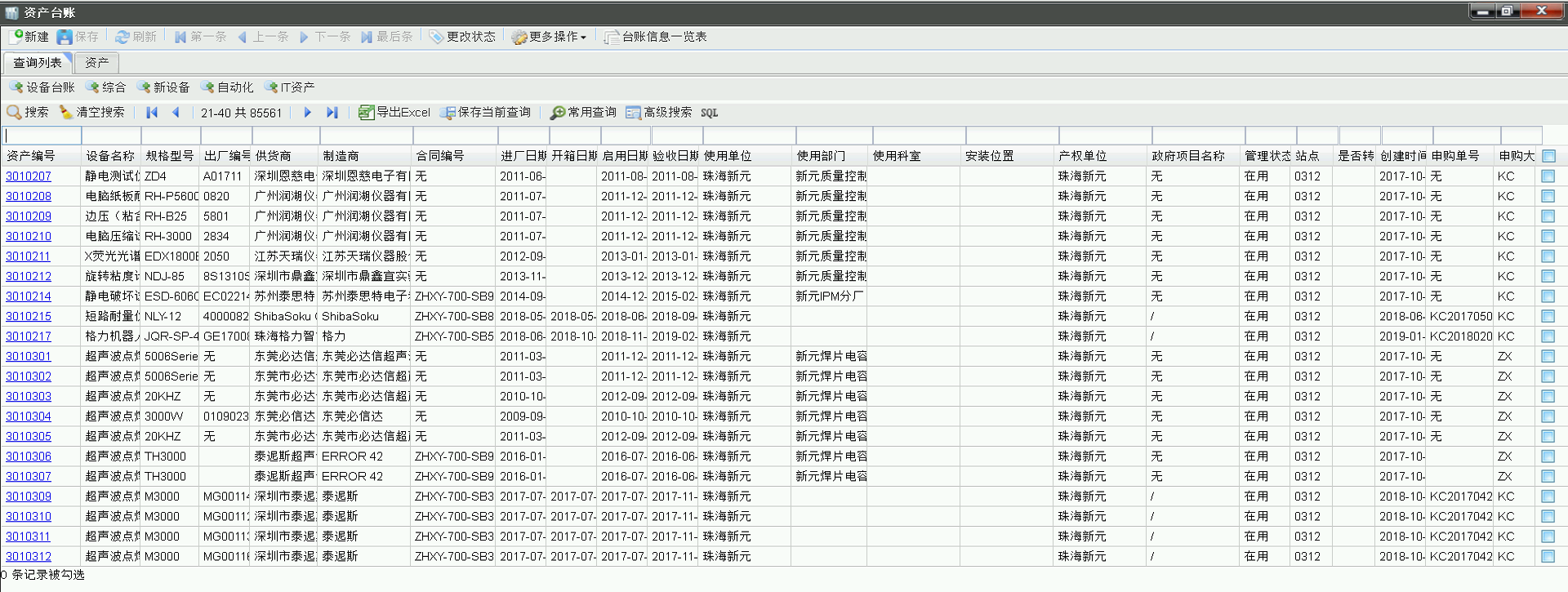
(6) Equipment change management
Equipment change management mainly includes 9 processes including equipment scrapping, fixed asset transfer, equipment allocation (internal transfer), equipment transformation, equipment outsourcing maintenance, equipment storage (enablement), equipment borrowing, equipment leasing, and equipment warranty performance.
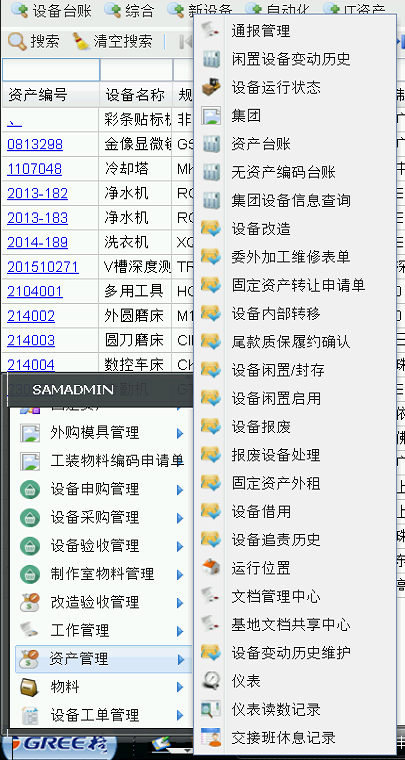
(7) Routine maintenance and management of equipment
The daily maintenance and management of equipment includes three categories: equipment fault handling, equipment professional inspection, and equipment maintenance.
malfunction repair:
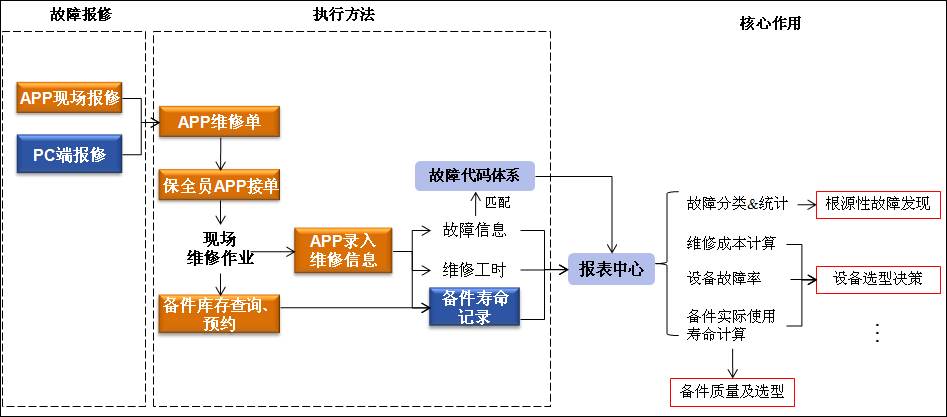
The current average daily number of trouble tickets is about 200.
Professional spot inspection and maintenance design scheme:
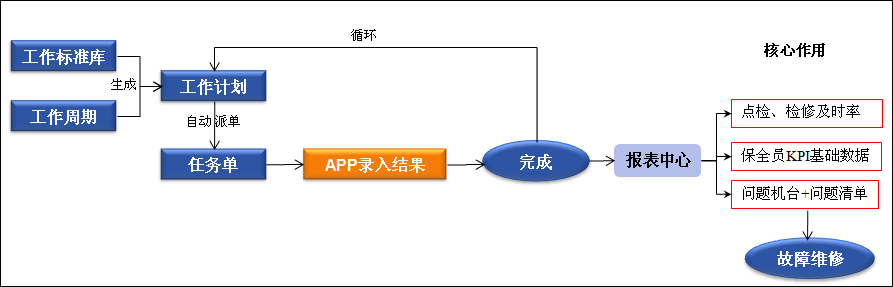
APP interface design:
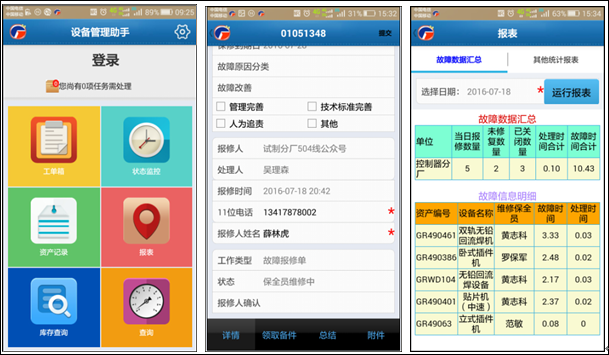
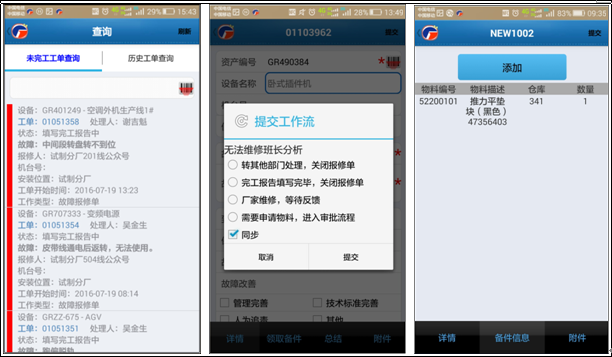
PC-side trouble ticket interface:
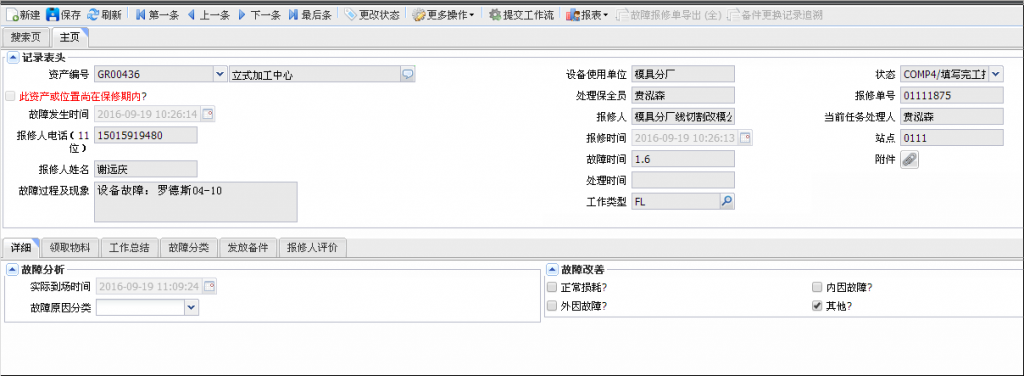
PC-side maintenance plan:
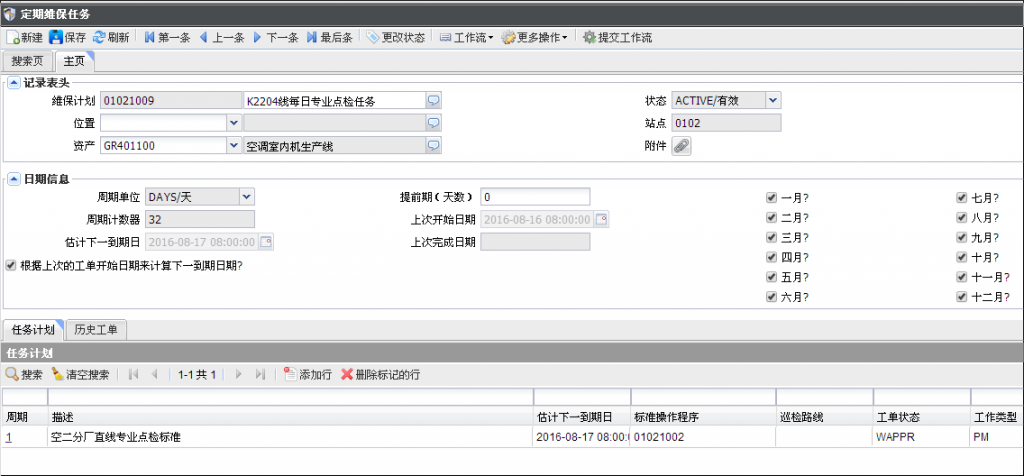
Fault code system:
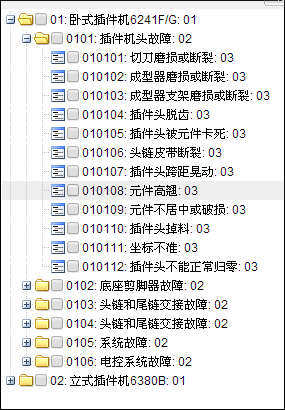
(8) Spare parts management
The group spare parts data platform realizes the group spare parts resource sharing and reduces the amount of repeated reserve inventory.
According to the optimized inventory model, management points such as safety stock, maximum stock and order point are set up to provide tool support for rationalizing stock structure and reduce stock reserve amount.
The mobile terminal is used for outbound and inventory to reduce the workload of spare parts administrators.
System spare parts module design scheme:
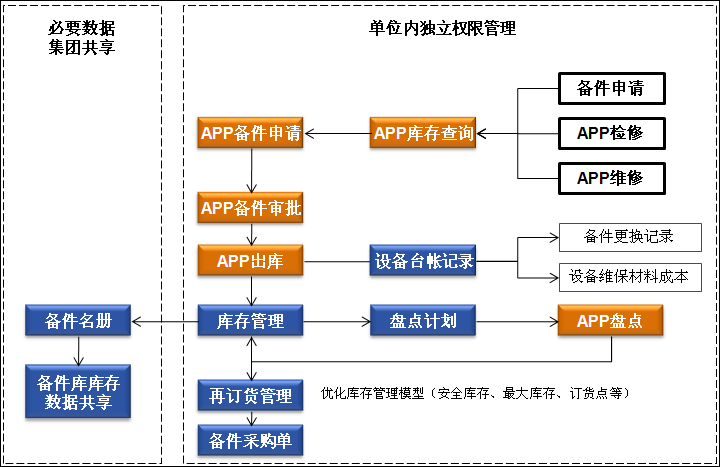
Spare parts information group sharing interface:
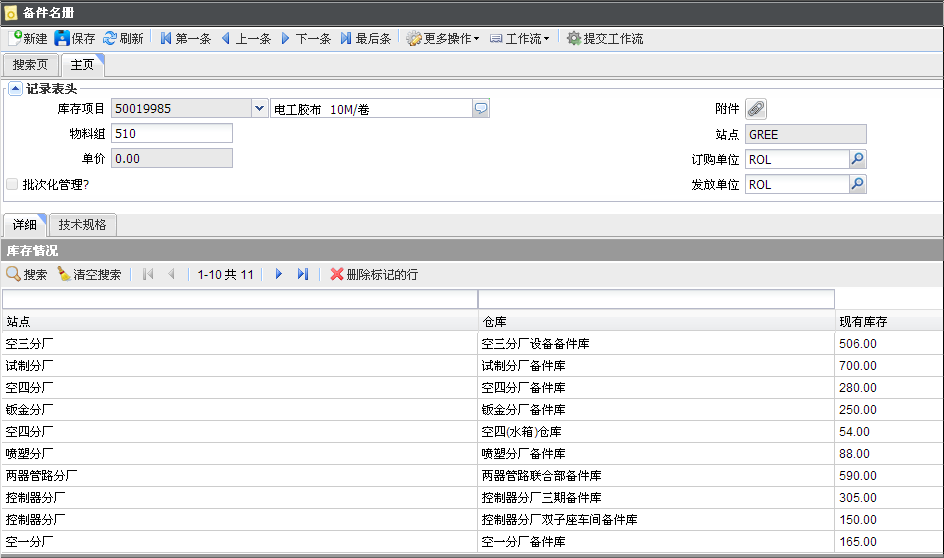
Spare Parts Inventory:
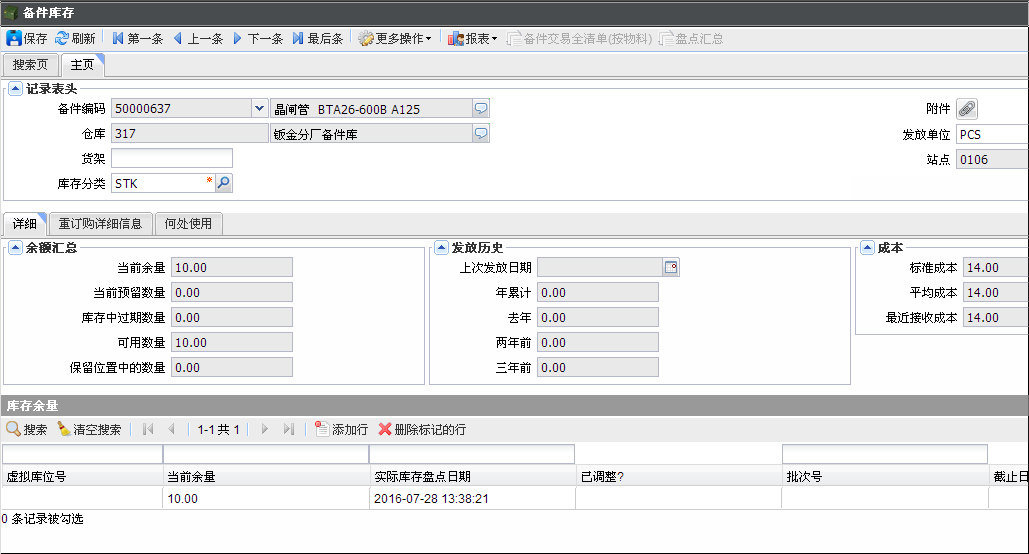
(9) Fixed asset management
Financial information such as the original value of assets and provision for impairment can be imported in batches.
It can automatically calculate the depreciation of fixed assets on a monthly basis by adopting different depreciation methods according to parameters such as asset type, service life, residual value rate, etc. .
The original value of the asset can be adjusted. After the original value is adjusted, the depreciation is automatically calculated according to the new original value every month.
It can automatically calculate the data of changes in the original value of assets, asset impairment provision, accumulated depreciation, net value, and fixed asset disposal caused by monthly asset transfer, scrap, return, etc.
It can realize asset verification and inventory by using mobile terminal online or offline, realize data download, upload, generate inventory report, create inventory result processing approval process through mobile terminal, and track inventory result processing.
Realize report statistics and query functions, including fixed asset ledger report, asset increase and decrease change report, asset depreciation schedule and other financial reports.
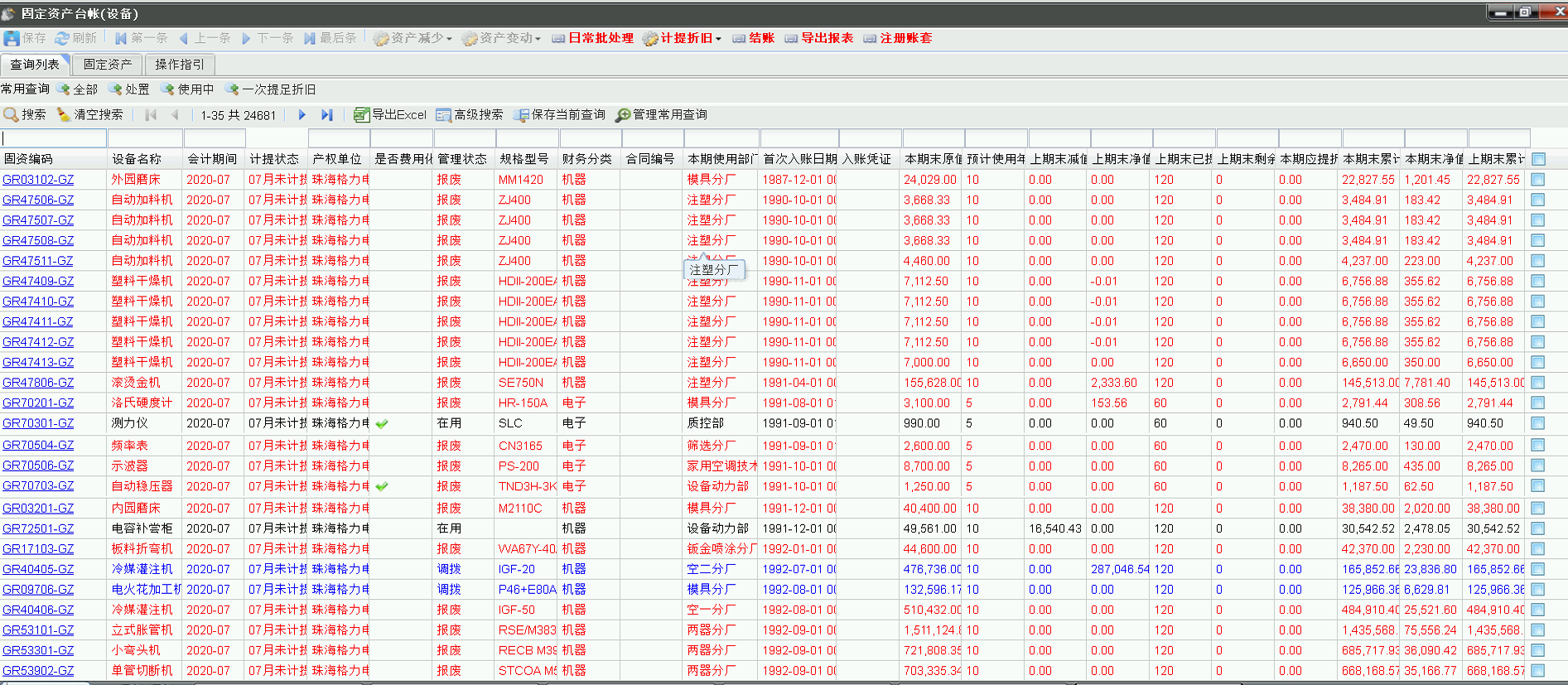
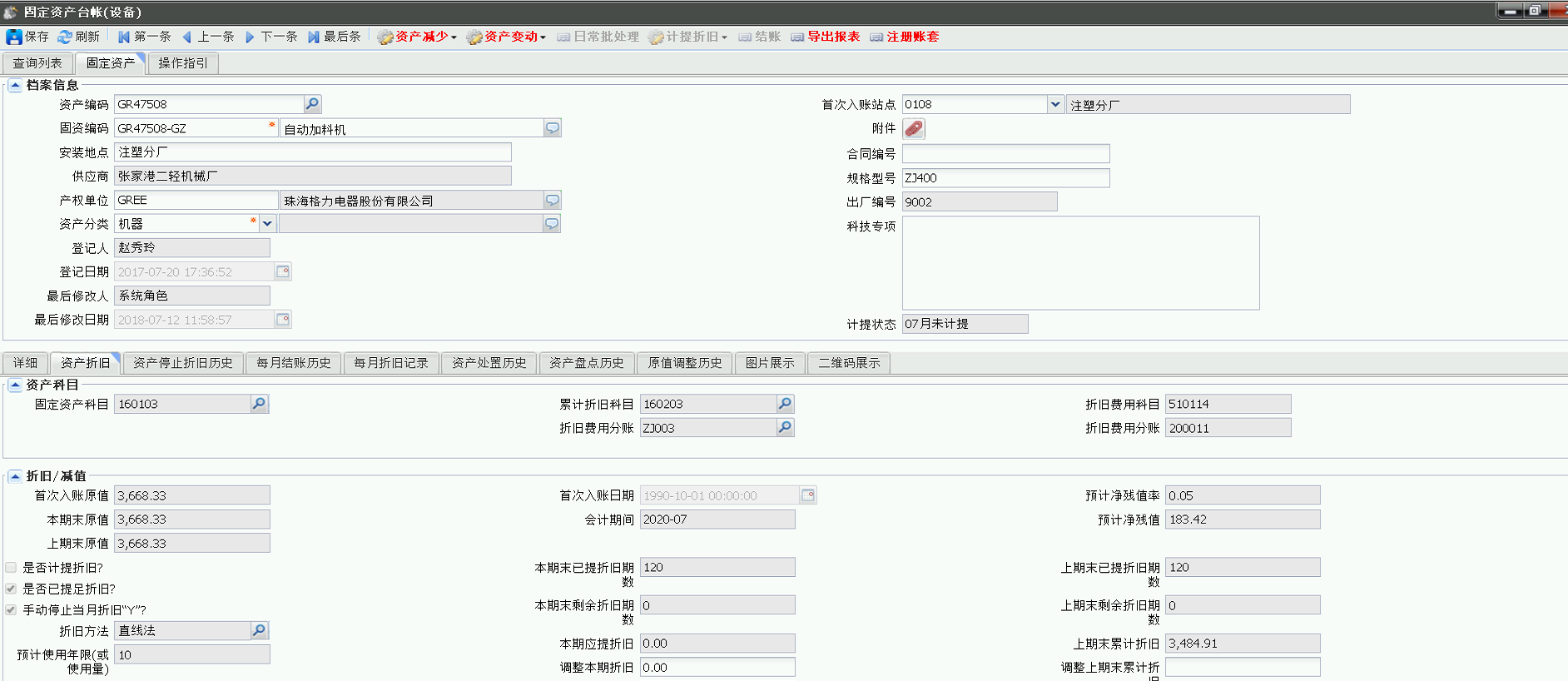
Inventory interface:
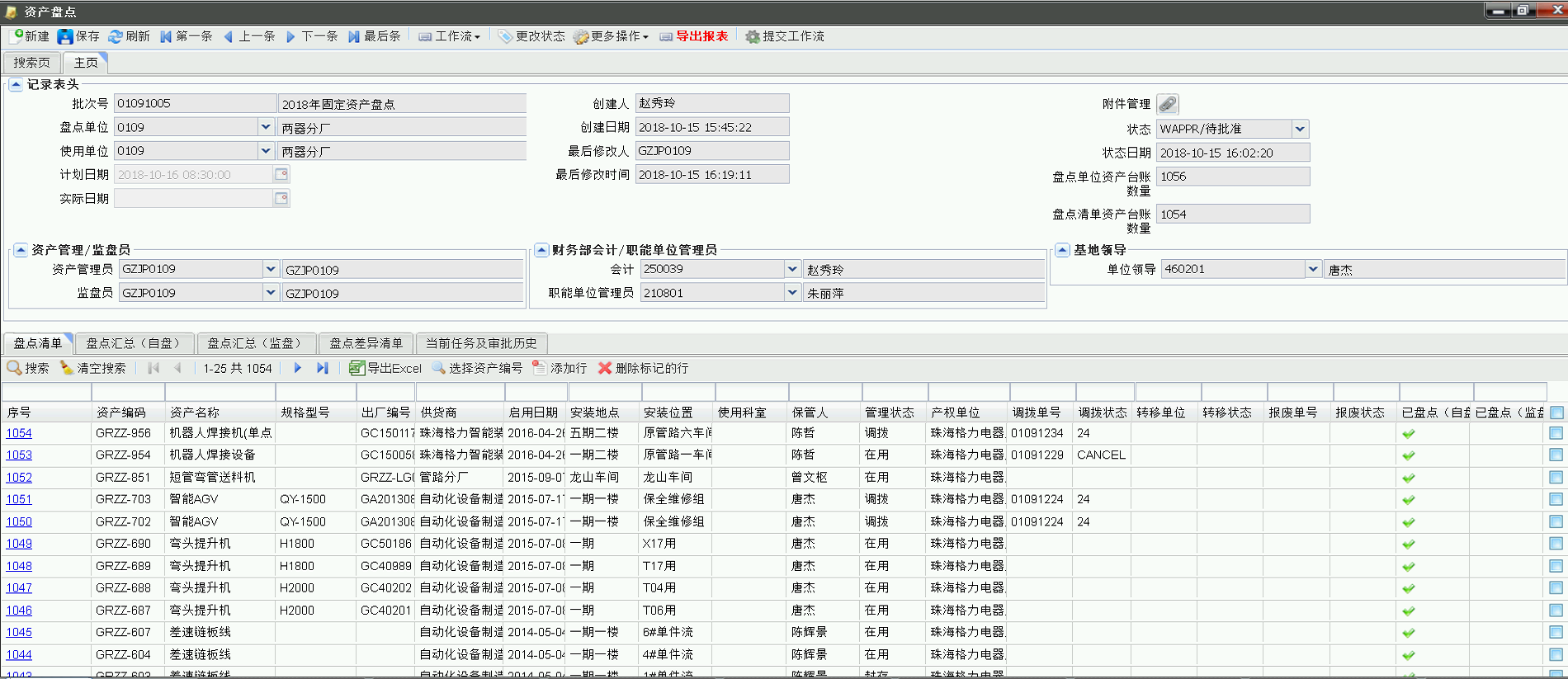
Summarize:
1. It is applied to the equipment management of the whole group to realize the standardization of equipment management and information sharing of the whole group.
2. The realization of equipment from budget purchase, approval and review, technical requirements, and equipment selection decision support in the information system is a blank area in the current equipment management system and has industry originality.
3. Set up equipment procurement module and supplier bidding management module, so that equipment purchase demand and procurement management can be realized in the same system platform, ensuring high consistency between demand and procurement, and innovative application in the industry.
4. Equipment management The introduction of APP terminal application to assist management can greatly improve the timeliness, accuracy and speed of data entry in equipment maintenance.