Project Background:
Hang Lung Group was established in 1960 and is one of the mainstream real estate developers in Hong Kong. Its main nature is the integration of real estate and property. Its properties include Shanghai 66 Plaza, Shanghai Grand Plaza 66, Shenyang Imperial City 66 Plaza in a total of 10 cities. Hong Kong properties including Causeway Bay Fashion Walk, Hang Lung Centre in Causeway Bay, The Peak Galleria at The Peak, and Kornhill Plaza in Quarry Bay.
The Group has introduced the SAMEX EAM enterprise asset management system since 2016 for independent management of different cities and regions. The main functions include:
1) Asset and facility ledger
2) Tenant information
3) Inventory materials
4) Daily inspection
5) Maintenance work order
6) Customer Service
7) Energy Management
8) Defect management (for new construction and decoration acceptance)
9) Contract management
10) Decoration management
Before using SAMEX EAM, the tenants of the property management of the group called the customer service, and then the customer manually recorded the problem and notified the corresponding personnel to solve the problem. There may be omissions in the middle, or the response was not timely. At the same time, the assets and location records were recorded. Incomplete records may also be missed. Meter reading statistics and employee performance appraisals all require manual use of excel calculations, which greatly reduces efficiency and accuracy.
Solution:
Use the SAMEX system to efficiently and quickly respond to tenants’ problems, and quickly create work orders for problems that need to be repaired and deal with them in a timely manner. Among them, SR (Service Request) is used to record the tenant’s complaints, service application, maintenance application and other issues, and provide records of service return visits after the service is completed to meet the needs of customers. WO (Fault Work Order) is used to submit a maintenance application. If a fault is found during the daily inspection process, the work order should be submitted in time, and the personnel of the corresponding work group will be notified to deal with it. SR+WO (service application + maintenance work order), the tenant submits a repair service request, the customer service staff records the type of service requested by the customer, and submits the corresponding work order, which is convenient for timely maintenance and feedback to the tenant.
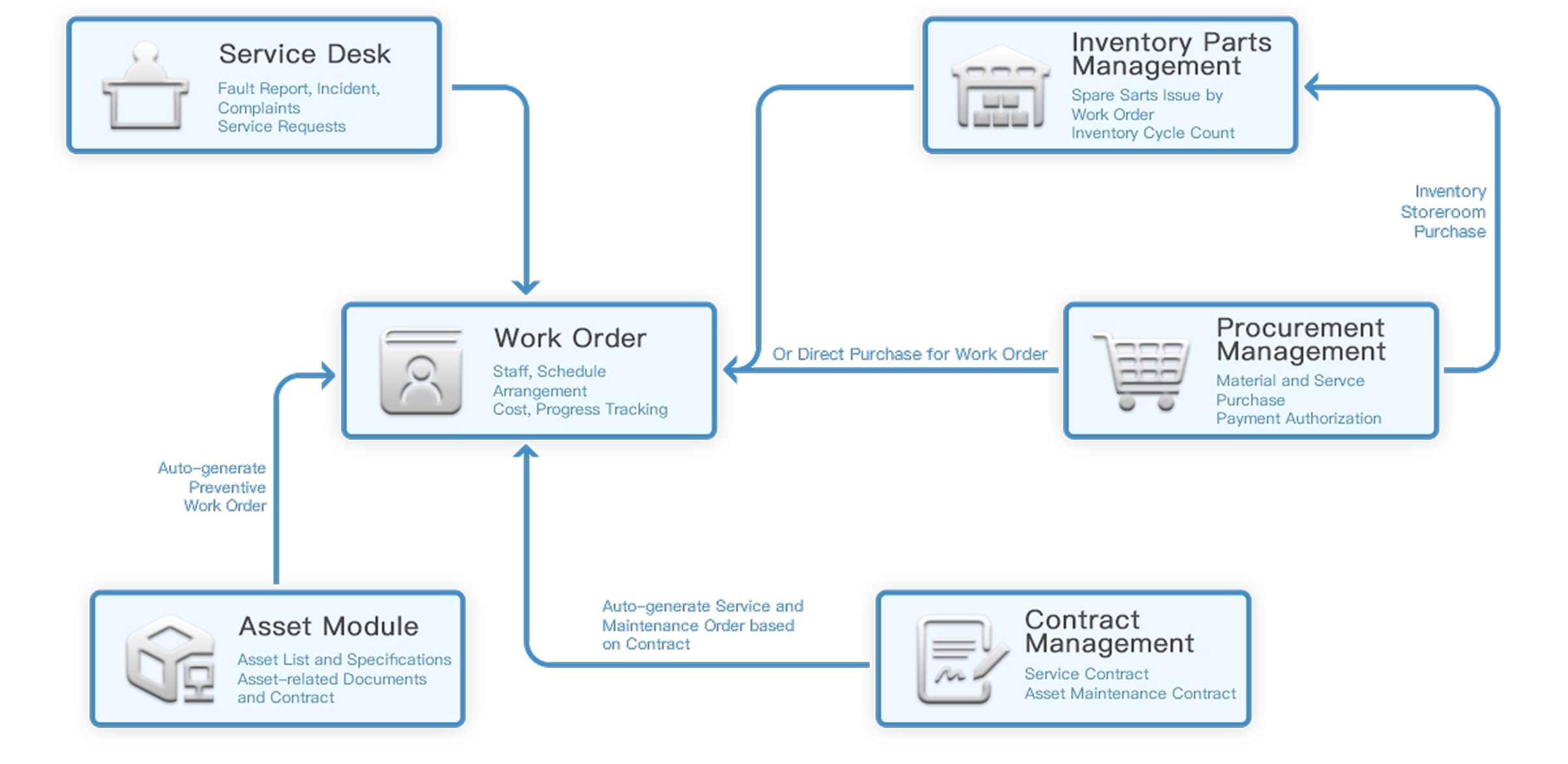
Use reports for efficient statistics, personnel work efficiency, work order statistics, energy analysis, and more.
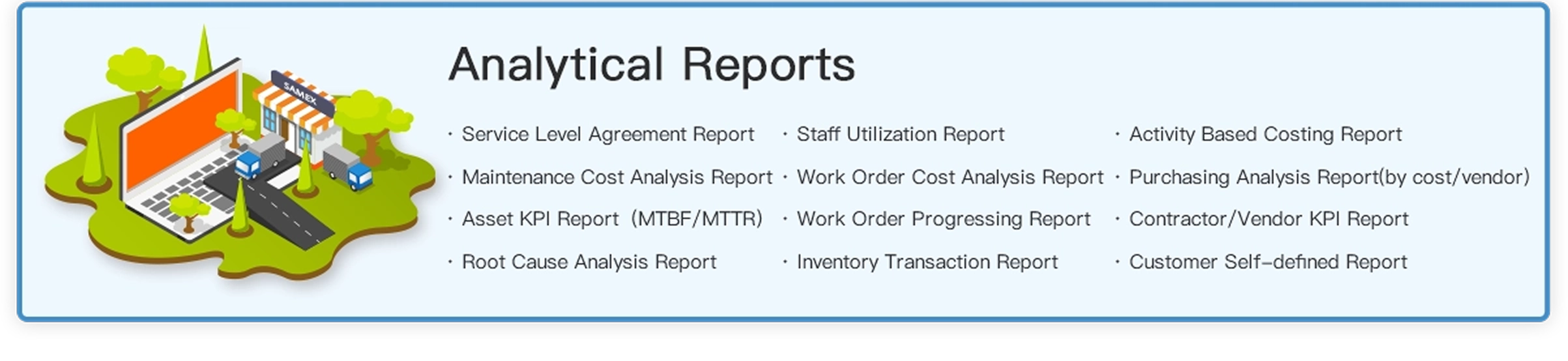
Implementation module:
3.1 Asset ledger
Asset list, according to the built-in multi-site function of the system, the group uses each city or region as an independent site to manage assets in a unified manner according to authority, and the system provides the import function of assets to import asset statistics in a unified manner.
In the asset details, define the location of the asset and the operating status of the asset, and manage the spare parts, instruments, technical specifications, maintenance history and maintenance history of the asset.
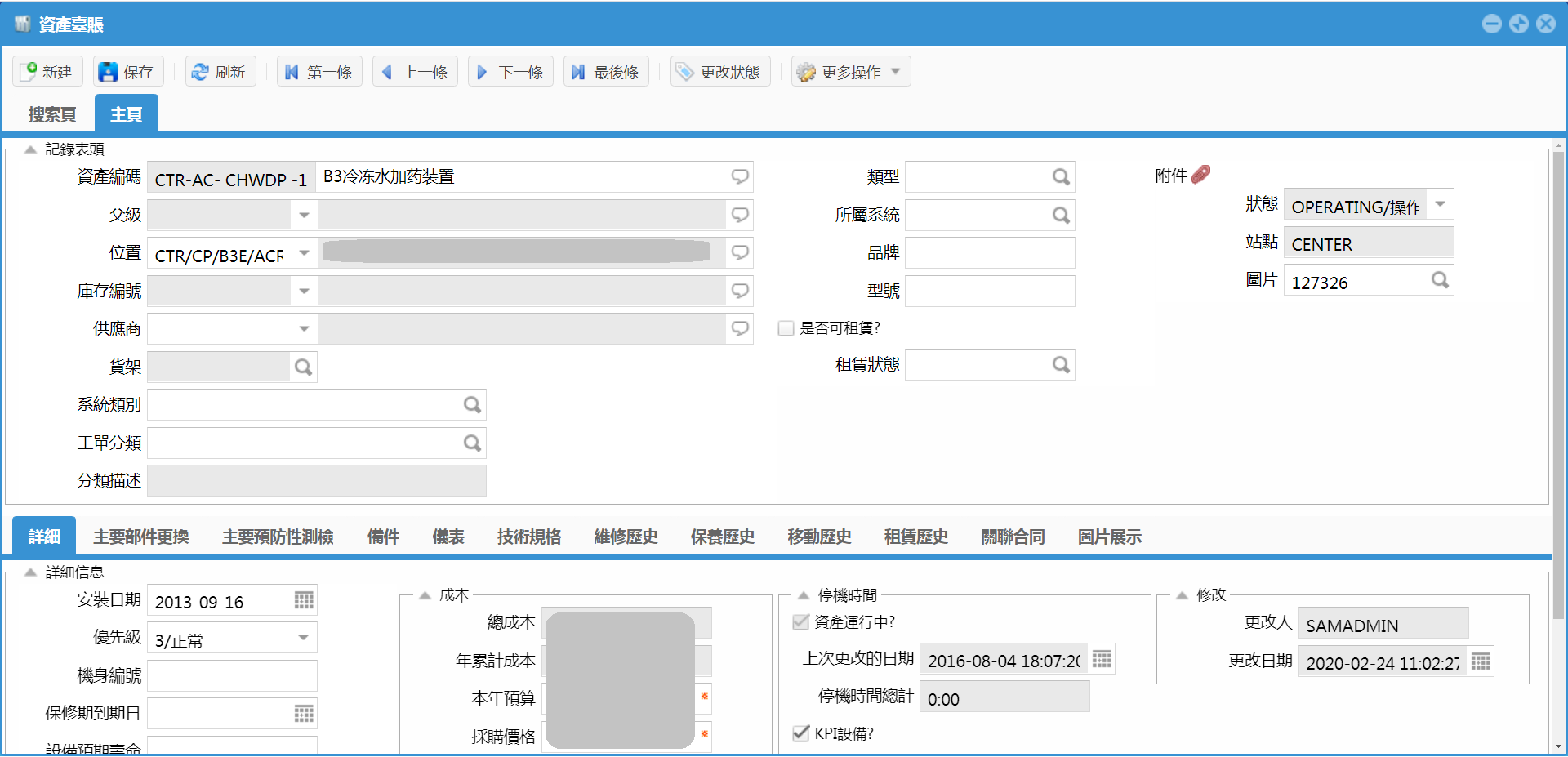
3.2 Instrumentation and energy management
The system defines different instrument types, as well as the reading unit of the instrument, and cooperates with the location to achieve energy consumption management at different locations. In energy management, imported energy reading records are provided to automatically calculate energy increments. At the same time, one-stop system auditing and repeated confirmation of meter readings are added to achieve efficient and accurate energy source data management.
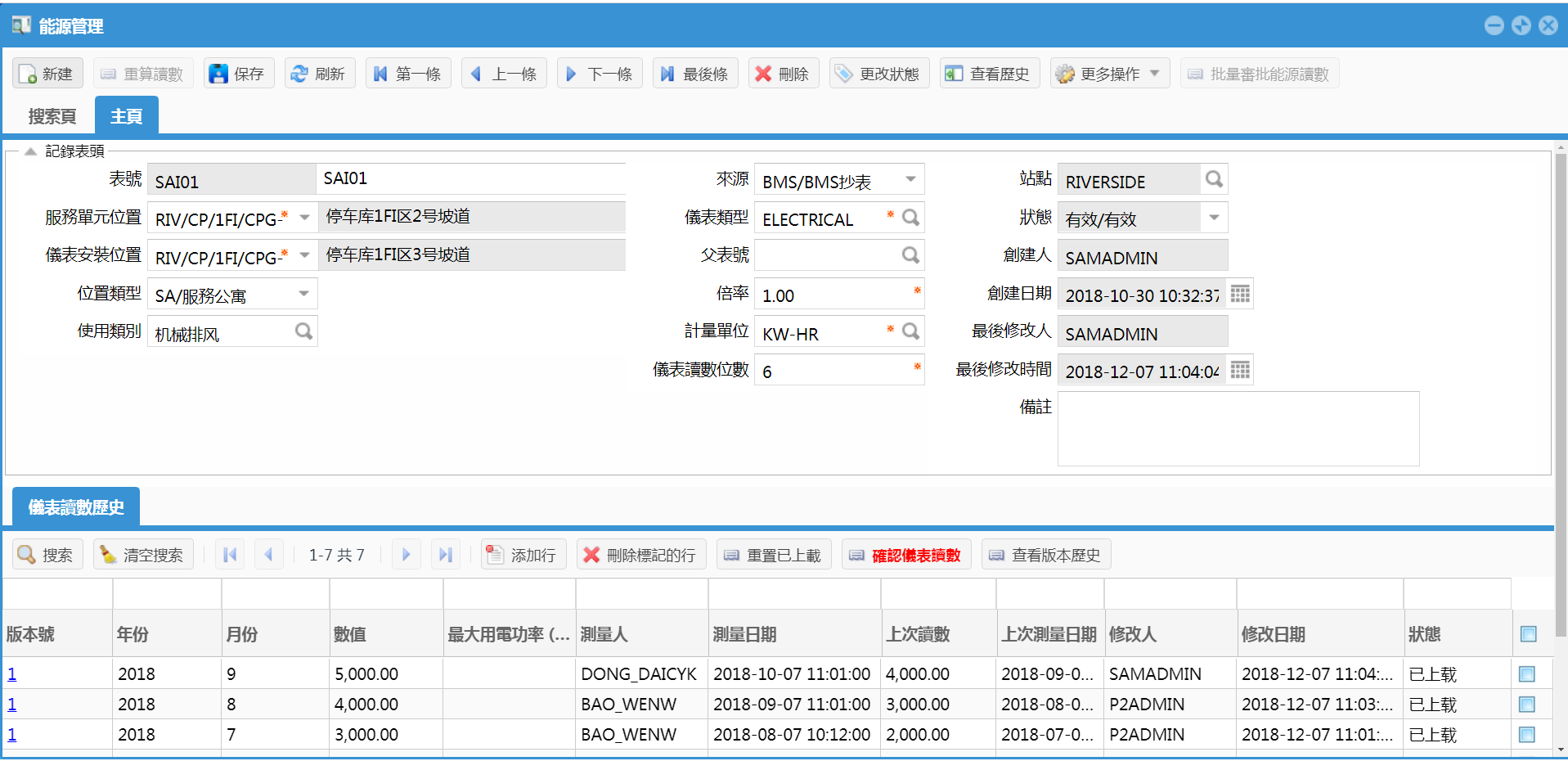
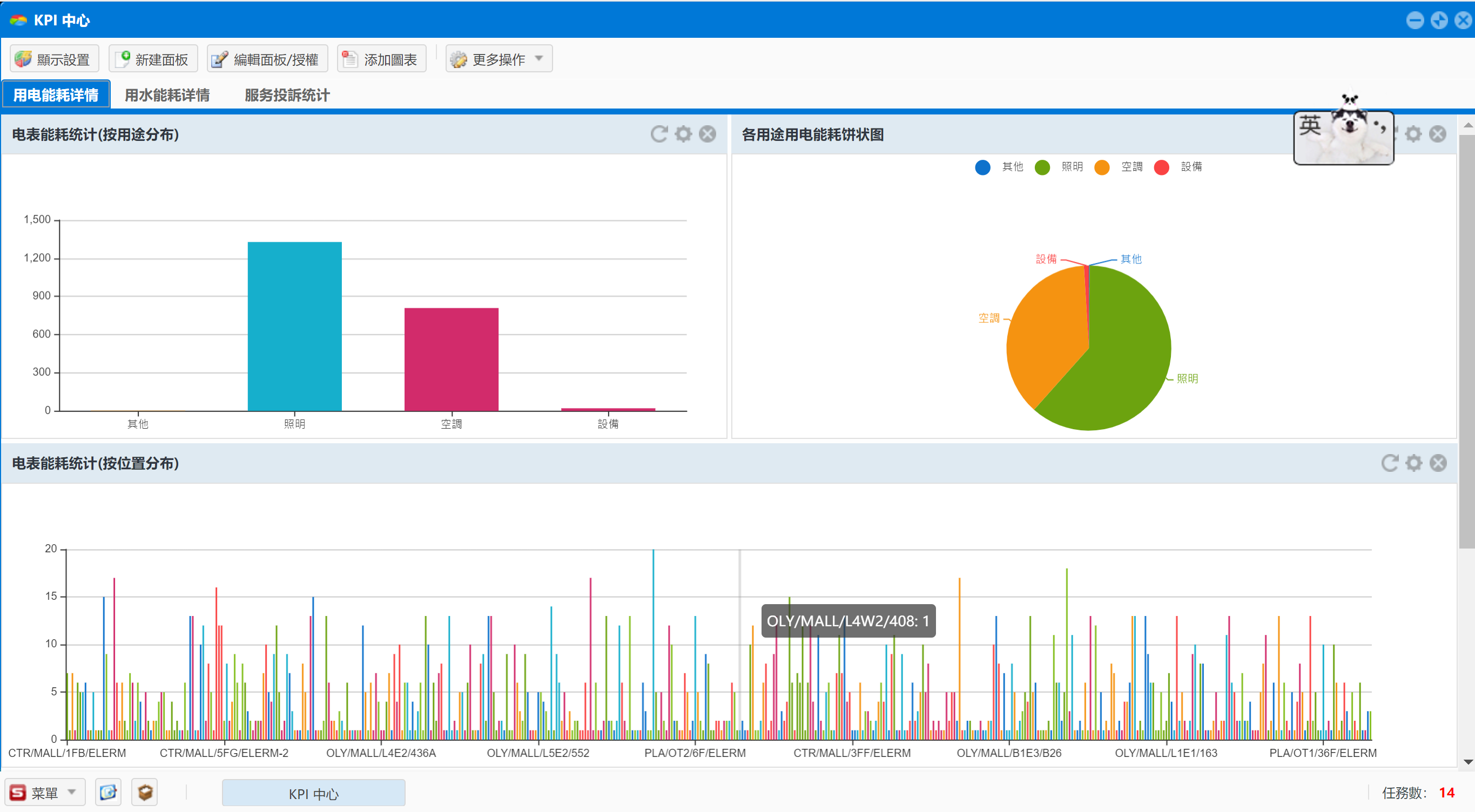
3.3 Warehouse, material, inventory management
Define the warehouse in the website, and define the spare parts, accessories and other items that need to be used in daily maintenance in the material application, and the inventory management application will manage the storage, so as to check the shelf, balance, reservation, etc. of the material in real time, and set the inventory at the same time Early warning, when the quantity is less than the warning value, timely purchase and replenish.
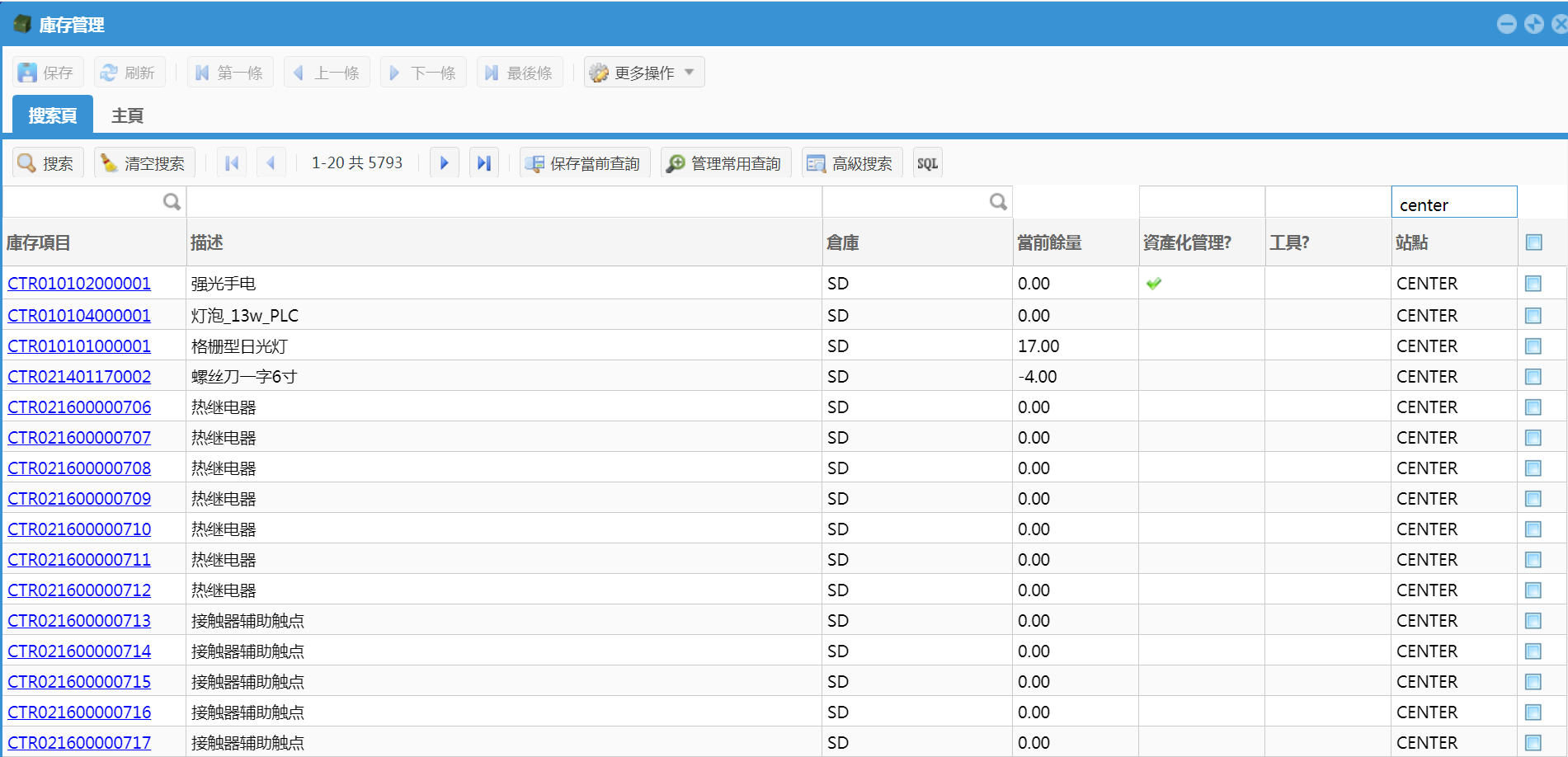
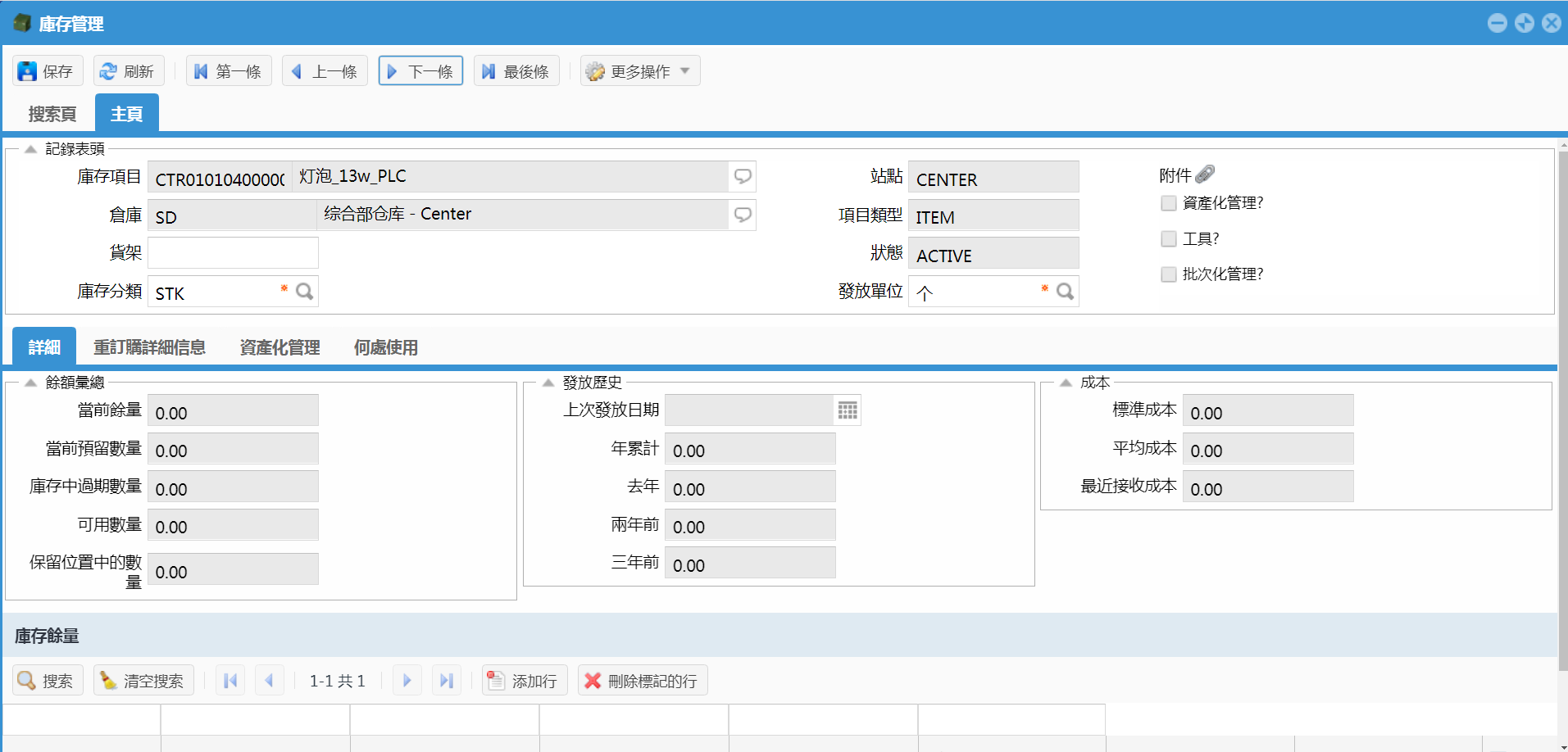
3.4 Tenant, Service Application
Manage tenant information in the tenant. Tenant Location, Tenant Unit Number, Tenant Name, Contact Person, etc.
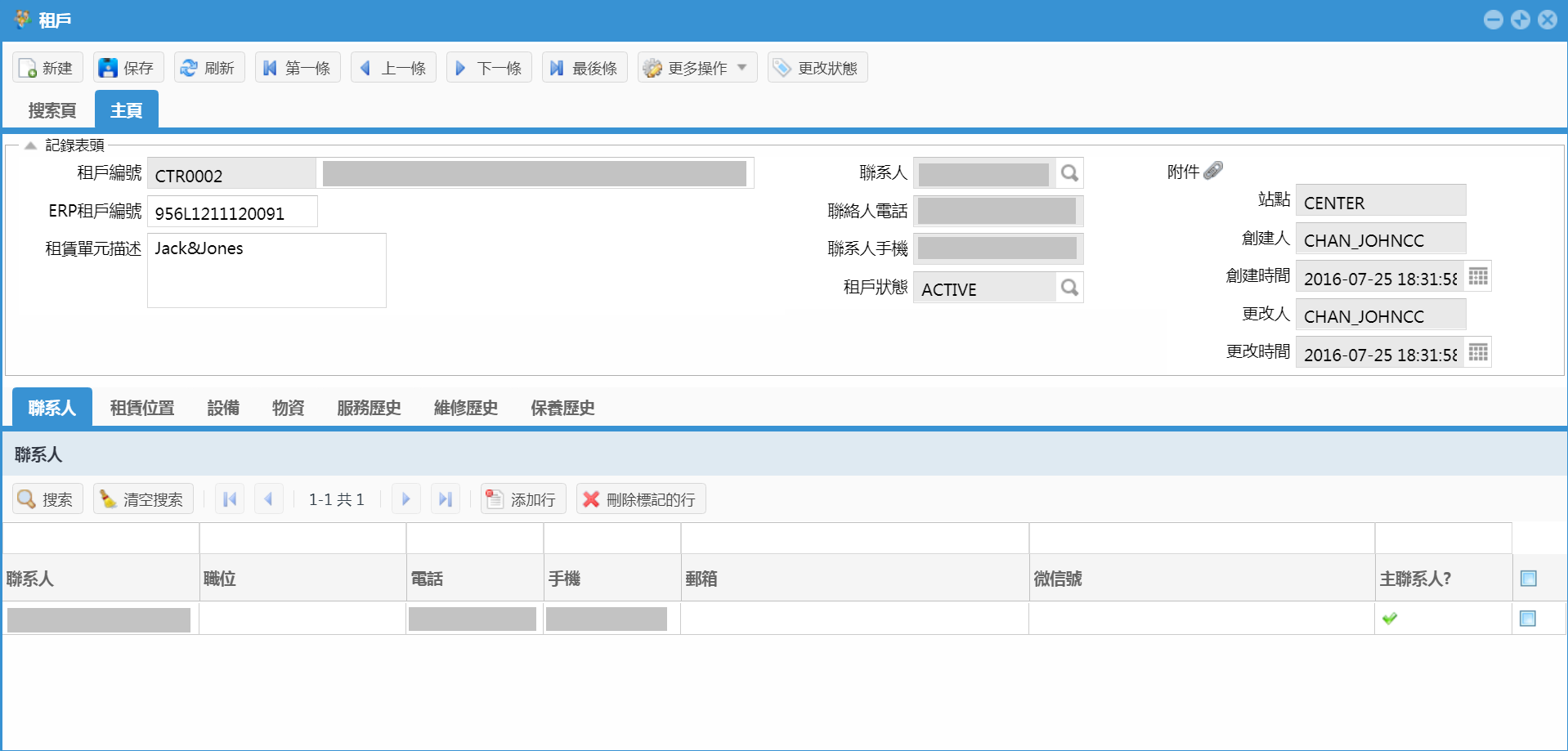
When a tenant submits a service application, the front desk customer service records the tenant’s request in the service application application according to the tenant’s description, binds the service application record to the tenant according to the information provided by the tenant, and specifies the tenant’s service request category. Automatically determine the type of service request (service or repair), and define the corresponding response time according to the emergency situation of the request.
Service application process (first determine whether the service request belongs to the repair category, and then the customer service personnel take the order -> provide the service -> complete the charge and return visit, in order to ensure the customer service experience, before submitting it to the supervisor for review, you must first complete the customer service return visit , in order to track and improve, to provide better service for customer service).
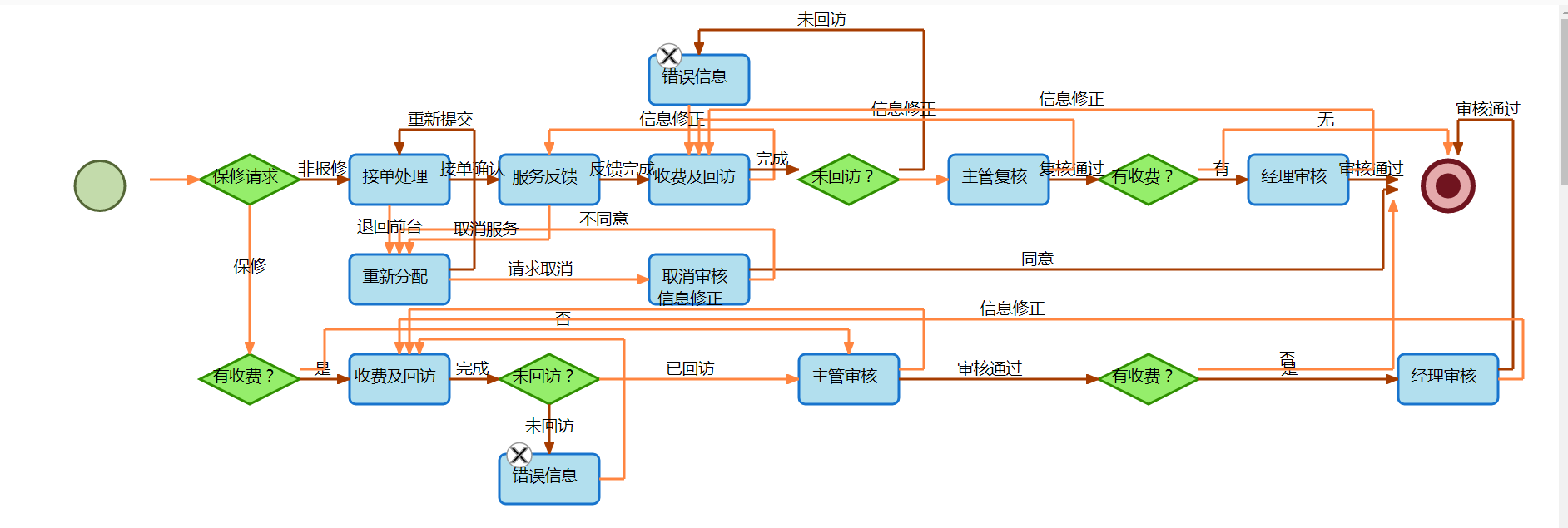
Service Request Master Record:
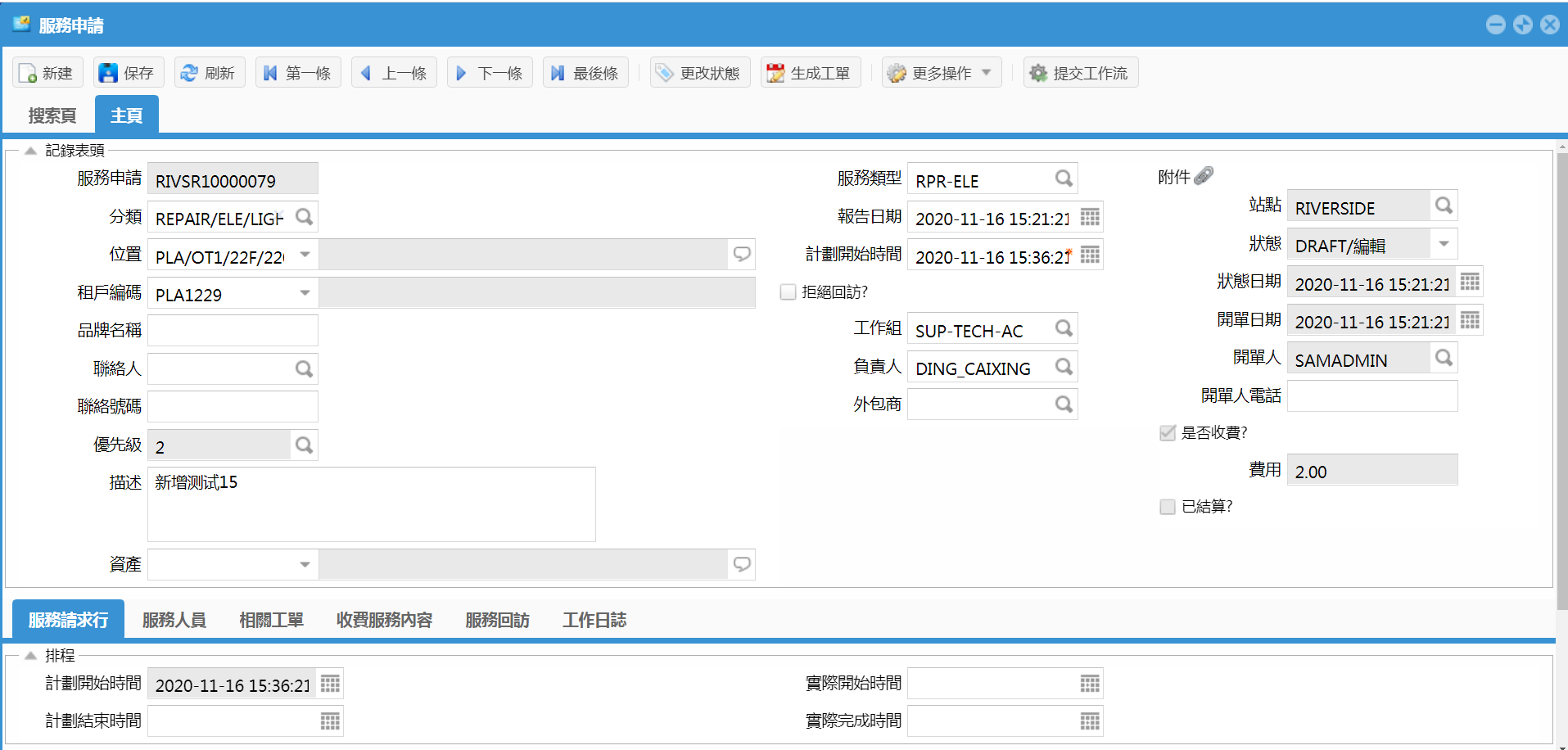
The definition of service application classification, except for the repair application category, all belong to the service application category, and the repair application needs to create an associated maintenance work order.
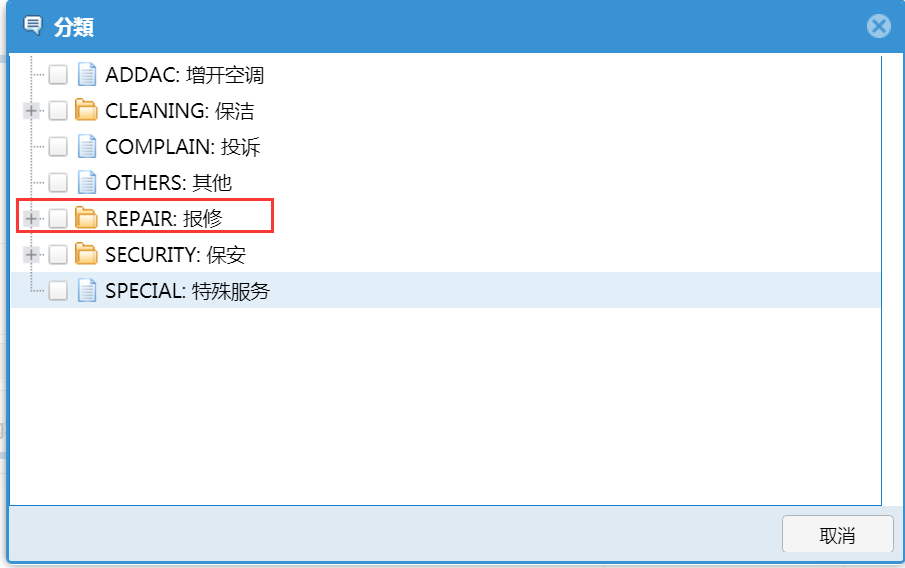
The priority order of service requests is set, and various priority orders are defined, and the time range that needs to be responded is set.
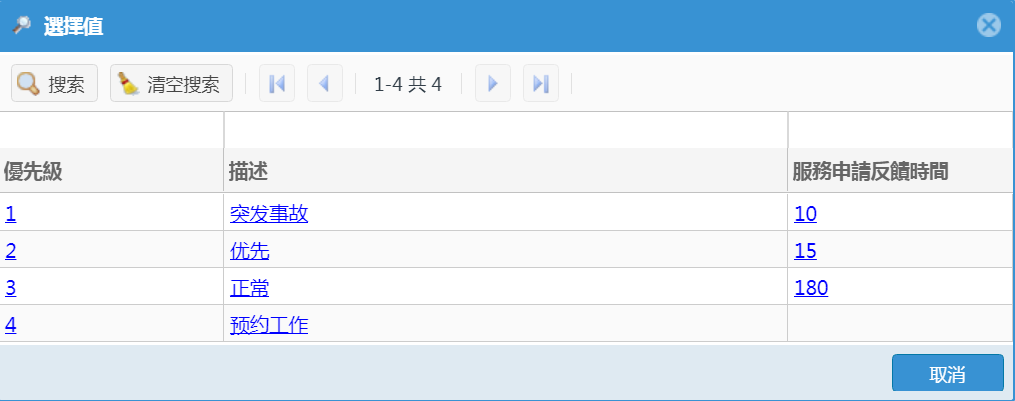
When the service request type is repair report type, you need to create a corresponding maintenance work order and submit it to the corresponding engineering group for maintenance processing. Create a work order as follows (click to generate a work order, select the category, and click to generate a work order).
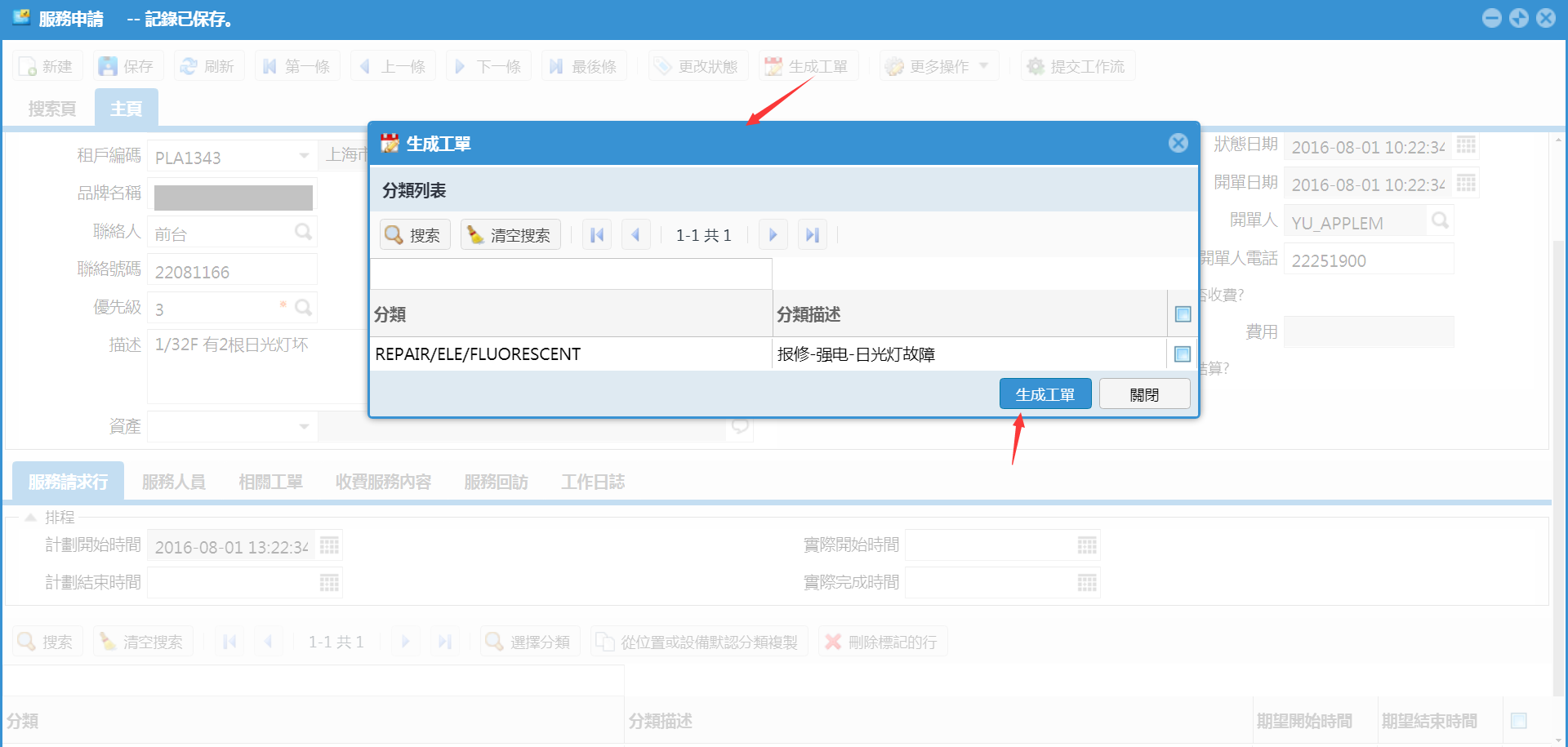
3.4 Trouble Tickets
It is used for repairing and billing, submitting the workflow to the corresponding engineering group, and recording the maintenance location, maintenance category, priority order, work group and other information.
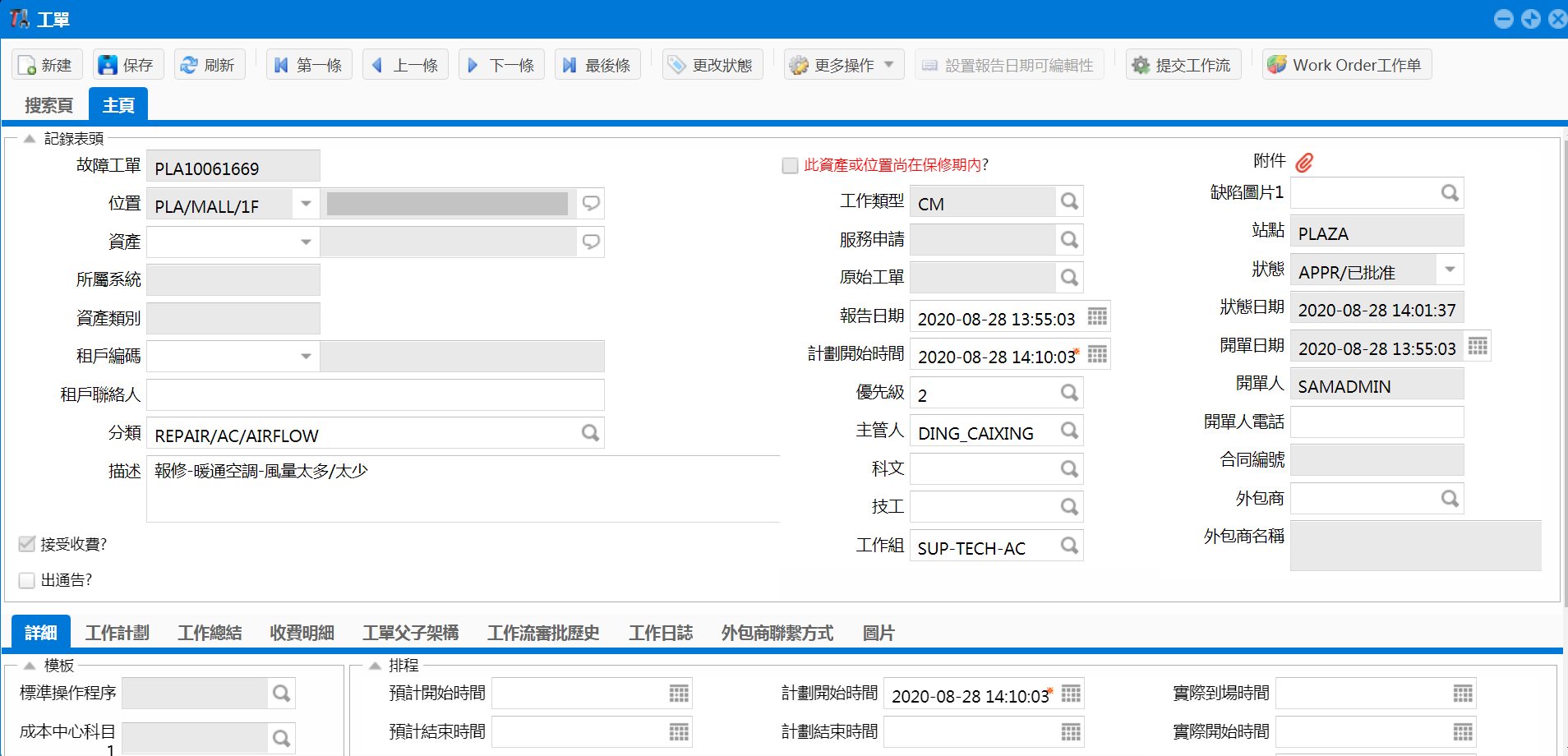
The fault work order process is as follows (the biller opens the bill -> the work team receives the order -> completes the plan filling -> the staff completes the task -> the manager reviews -> closes the work order), the maintenance staff completes the work and completes the work order When adding whether to fill in the staff and fault category, in order to record the performance appraisal of the staff.
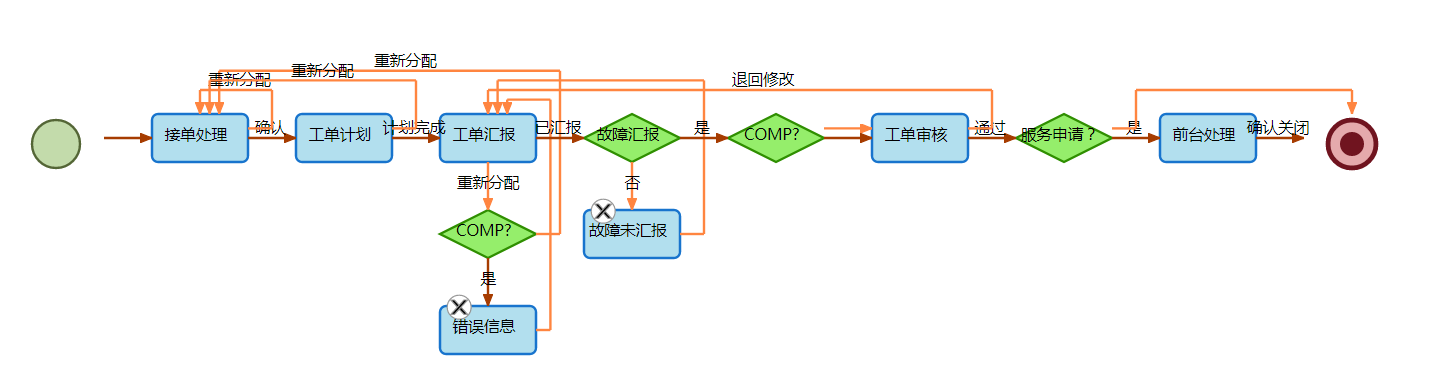
3.5 Inspection work order
Use the maintenance plan application to configure the start date and cycle of the inspection plan, and then change the status to valid. The system will execute the plan according to the settings and generate corresponding inspection work orders regularly.
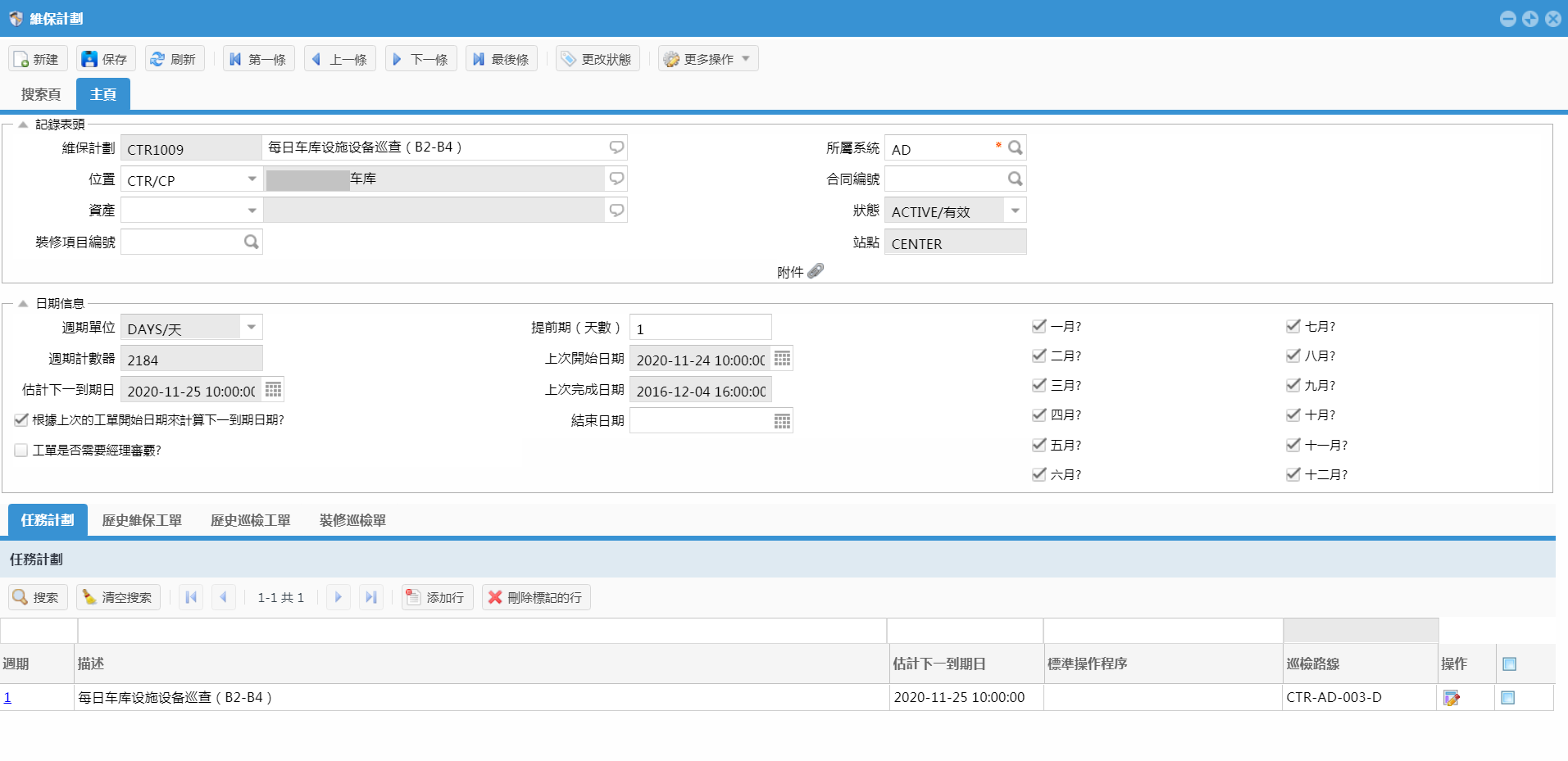
The work order type and inspection route are defined in the cycle, and the inspection steps are defined in the inspection route. For example, the A location needs to perform steps 1, 2, 3….
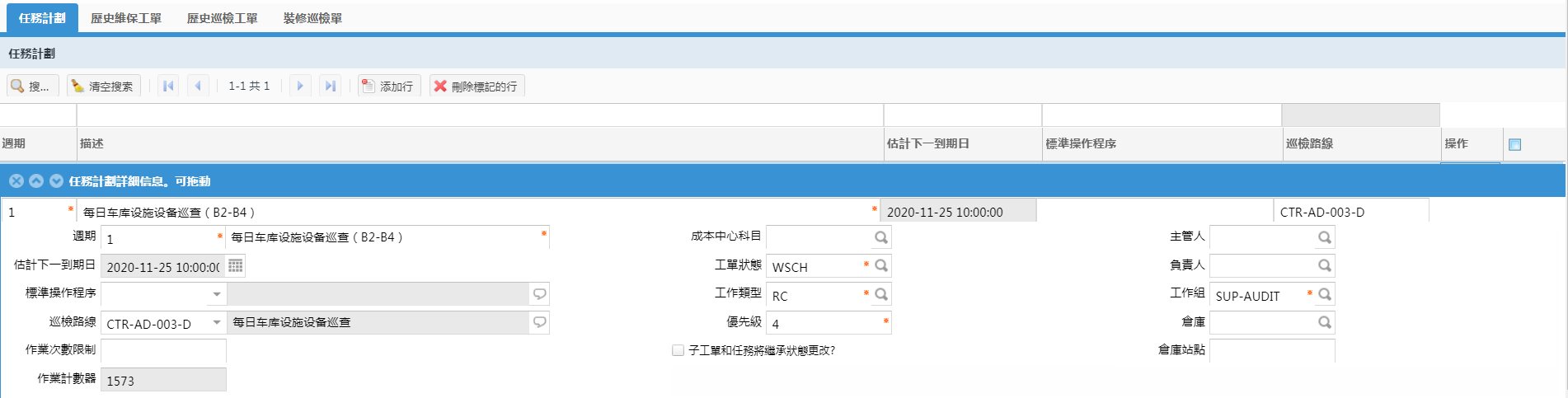
Definition of the inspection route (as shown in the figure representing the inspection on floors 1-6 of the shopping mall, each floor needs to execute the steps in the corresponding standard operating procedure).
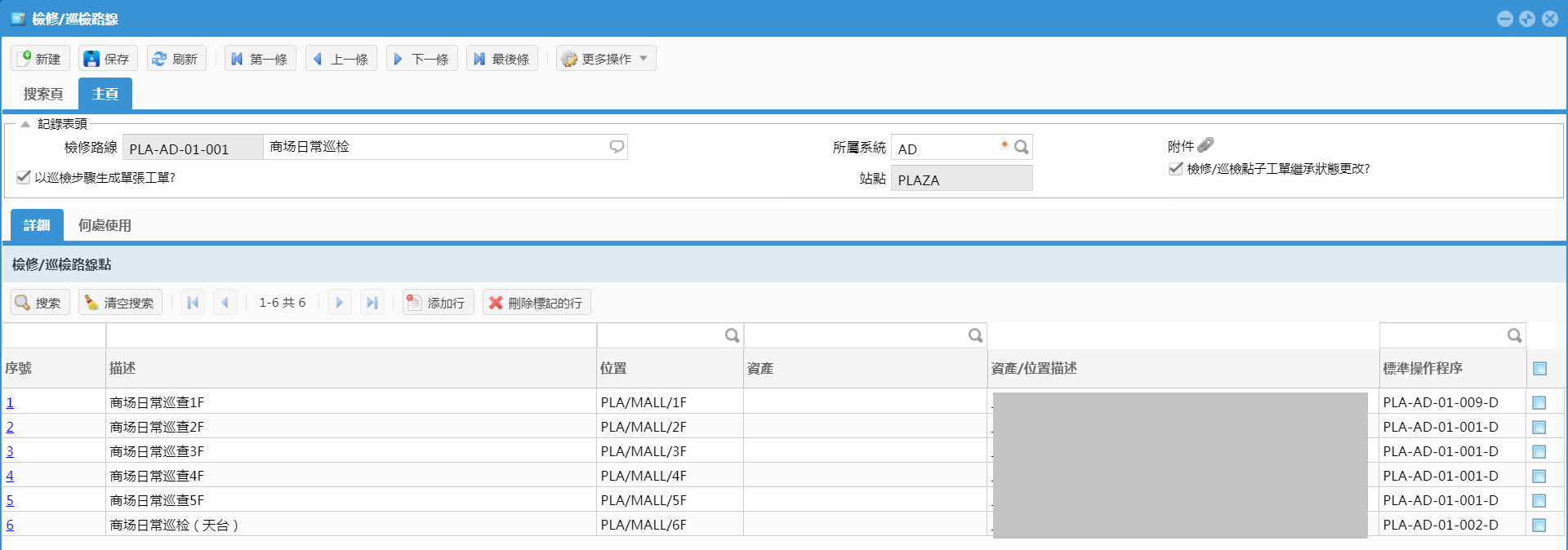
Standard operating procedures are defined as follows:
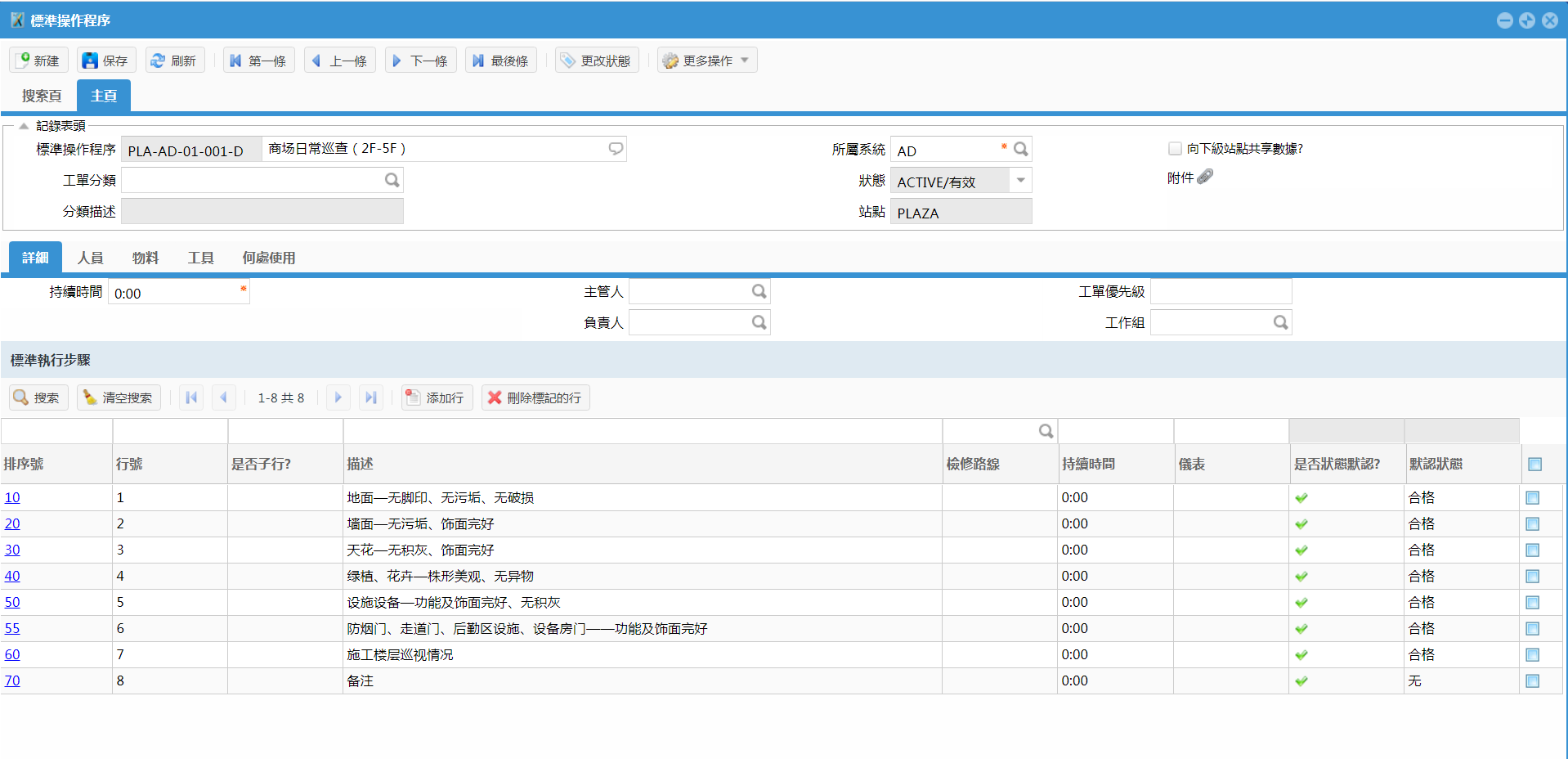
3.6 Incident reporting
For emergencies in shopping malls or office buildings, it is also necessary to record and follow up, so we have defined an incident reporting application to achieve tracking, record the description and content of the incident, and instant photo upload, follow-up matters, insurance follow-up, and follow-up. information, the cause of the accident, and the recipient address settings for sending notification emails.
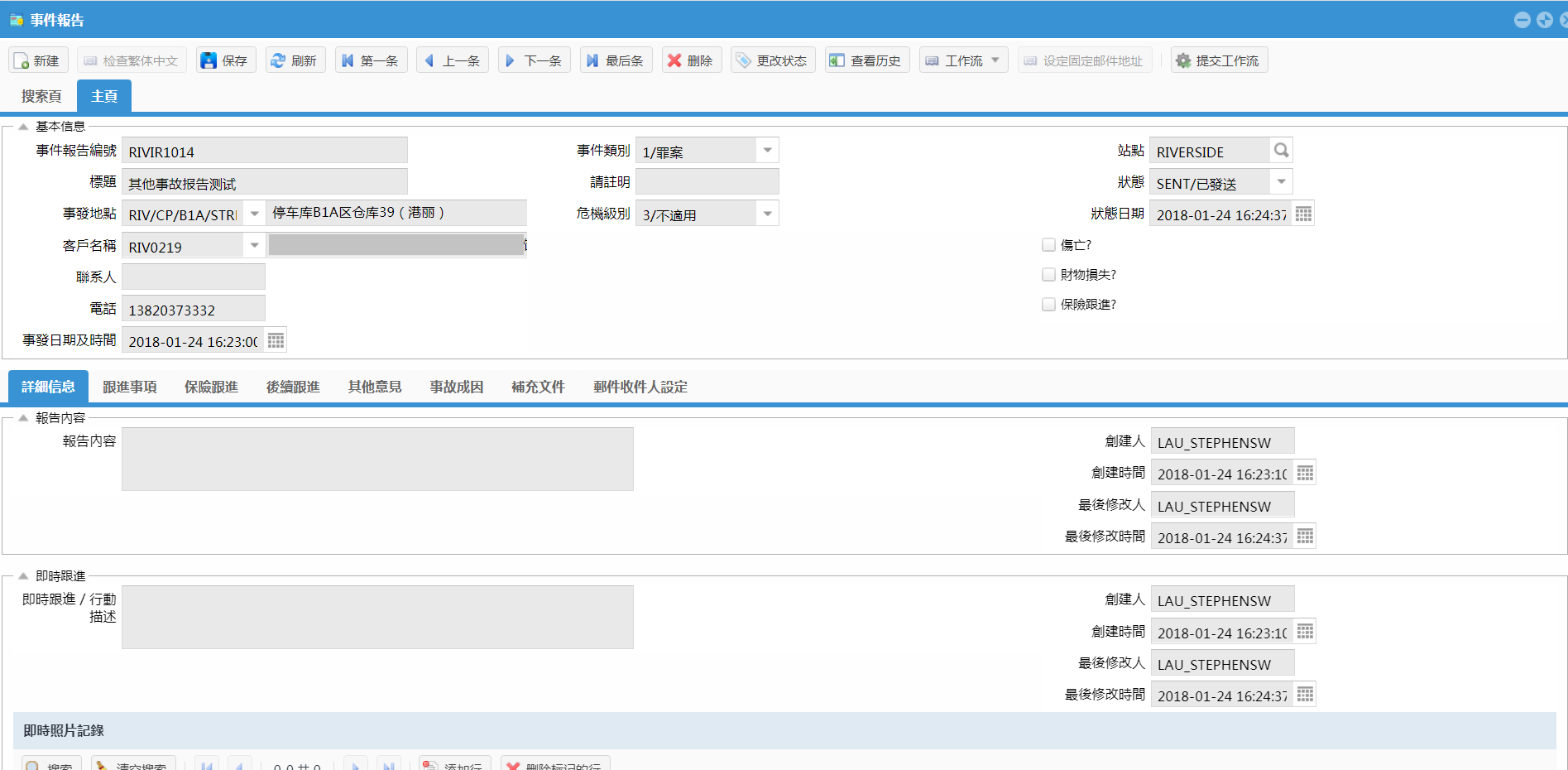
The incident reporting process is as follows (the reporter submits the incident report -> SD approval -> the reporter sends it to the general affairs department for review -> the affairs department fills in the cause of the accident and submits it to the head of the SD department for review -> closes the incident report after approval).

3.7 Decoration management
Decoration is a relatively common form in commercial building management. Regardless of whether the renovation task is from the tenant or the company itself, renovations are faced with several tasks: 1. Pre-application for renovations, including review of drawings, 2. Supervision during the execution of renovations.
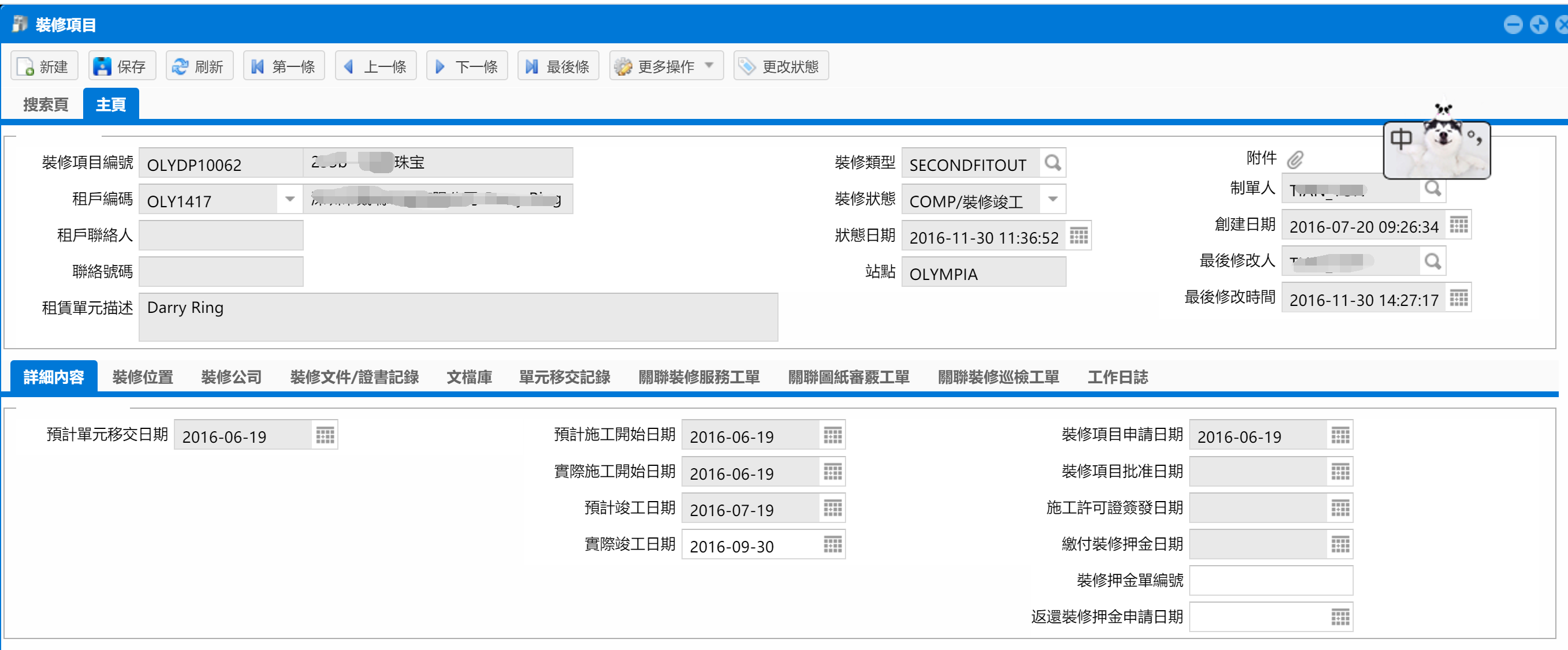
Summarize:
Large-scale traditional manufacturing industries including steel, mining, and metallurgy are technology- and asset-intensive traditional industries. An important feature of these enterprises is that the source of profits of the enterprise cannot be separated from the normal operation of these assets and equipment. Unplanned downtime means a suspension of corporate profits. However, like many other traditional manufacturing industries (such as power plants and energy companies, etc.), the management of these equipment has not received the attention it deserves in the enterprise.
Strengthening personnel management and improving equipment reliability is the only way for asset and equipment-intensive enterprises to improve production efficiency. In the face of such huge assets and equipment, enterprises must use professional EAM (Enterprise Asset Management, enterprise asset management) The system can be used for precise management, and the equipment reliability model can be quickly and effectively established, so as to improve equipment performance and increase production capacity.
SAMEX enterprise asset management system is a set of professional EAM solutions, the value it brings is mainly reflected in:
(1) Significantly reduce equipment maintenance costs (20% – 40% on average)
(2) Significantly reduce the equipment failure rate, shorten the equipment maintenance cycle on average, and prolong the equipment failure cycle (average 80% – 300%)
(3) Significantly reduce inventory costs, eliminate sluggish spare parts, and improve corporate inventory sharing and allocation capabilities
(4) Improve equipment reliability and reduce unexpected downtime losses
(5) Improve equipment performance and increase equipment output (15%-20% on average)
(6) Quickly establish equipment reliability mode to reduce unexpected downtime