EAM, short for Enterprise Asset Management, is a combination of software, systems, and services used to maintain and control operational assets and equipment. Its goal is to optimize asset quality and utilization throughout their lifecycle, increase production uptime, and thereby reduce operational costs.
In Toyota’s factories, assembly lines rolling out a new car every minute achieve “zero unplanned downtime” throughout the year. A mechanical parts manufacturer increases annual production capacity by 67% year-on-year. Behind these seemingly impossible achievements lies the same driving force—Enterprise Asset Management (EAM). As global manufacturing loses $647 billion annually due to equipment failures, EAM is becoming the key solution for asset-intensive organizations.
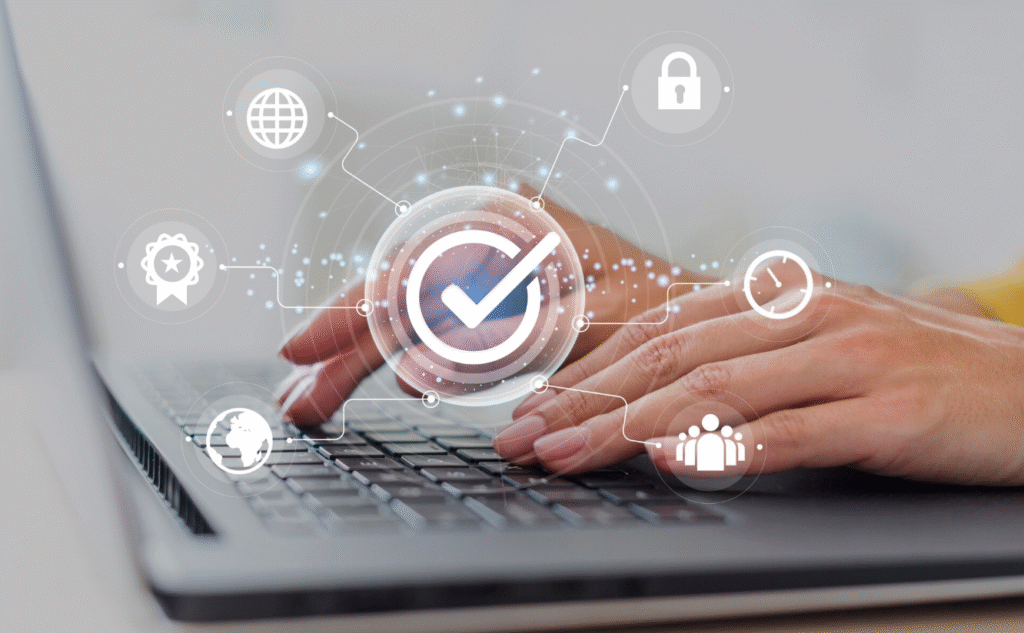
1.Efficiency Revolution
In the traditional industrial era, equipment management was like “the blind men touching an elephant”—fraught with high risks, costs, and error rates. For example, when a factory’s equipment suddenly failed, it took 48 hours to process paper work orders, resulting in a production line shutdown costing $26,000 per minute. EAM systems, however, change the game by building a digital network.
In the information age, EAM integrates equipment, machinery, and production systems—migrating from isolated legacy systems to a highly integrated platform. Work orders are digitized and automatically generated as part of routine equipment maintenance.
By maintaining real-time asset data and leveraging AI algorithms to predict failure probabilities, companies shift from “reactive firefighting” to “proactive prevention.” Gree Electric, a leading Chinese manufacturer, validated this transformation after implementing SAMEX EAM: equipment downtime decreased by 38%, and unexpected failures dropped by 70%. View successful cases of Gree using SAMEX EAM
Real-time monitoring of equipment status and performance metrics enables timely alerts and fault resolution, minimizing production interruptions. Effective management and maintenance enhance equipment reliability and stability, ensuring smooth production lines and boosting efficiency.
2.Cost Restructuring
Hidden costs in asset management are often staggering: A mining company had over $30 million tied up in spare parts inventory, 30% of which remained unused until equipment was scrapped. A thermal power plant wasted 18% of its total electricity due to boiler idling. EAM acts like a precision scalpel, targeting these pain points.
In operations, the system optimizes spare parts procurement by analyzing historical data, reducing inventory costs by 25%. In energy management, smart start-stop algorithms cut equipment idling time, saving an auto plant $1.4 million annually in electricity.
Moreover, EAM helps organizations track asset usage—location, status, maintenance records—enabling better utilization and avoiding underuse or overuse. It facilitates rational equipment scheduling, preventing over-purchasing or idle resource waste. Regular maintenance and timely repairs further prevent production halts and costly breakdowns, slashing operational expenses.
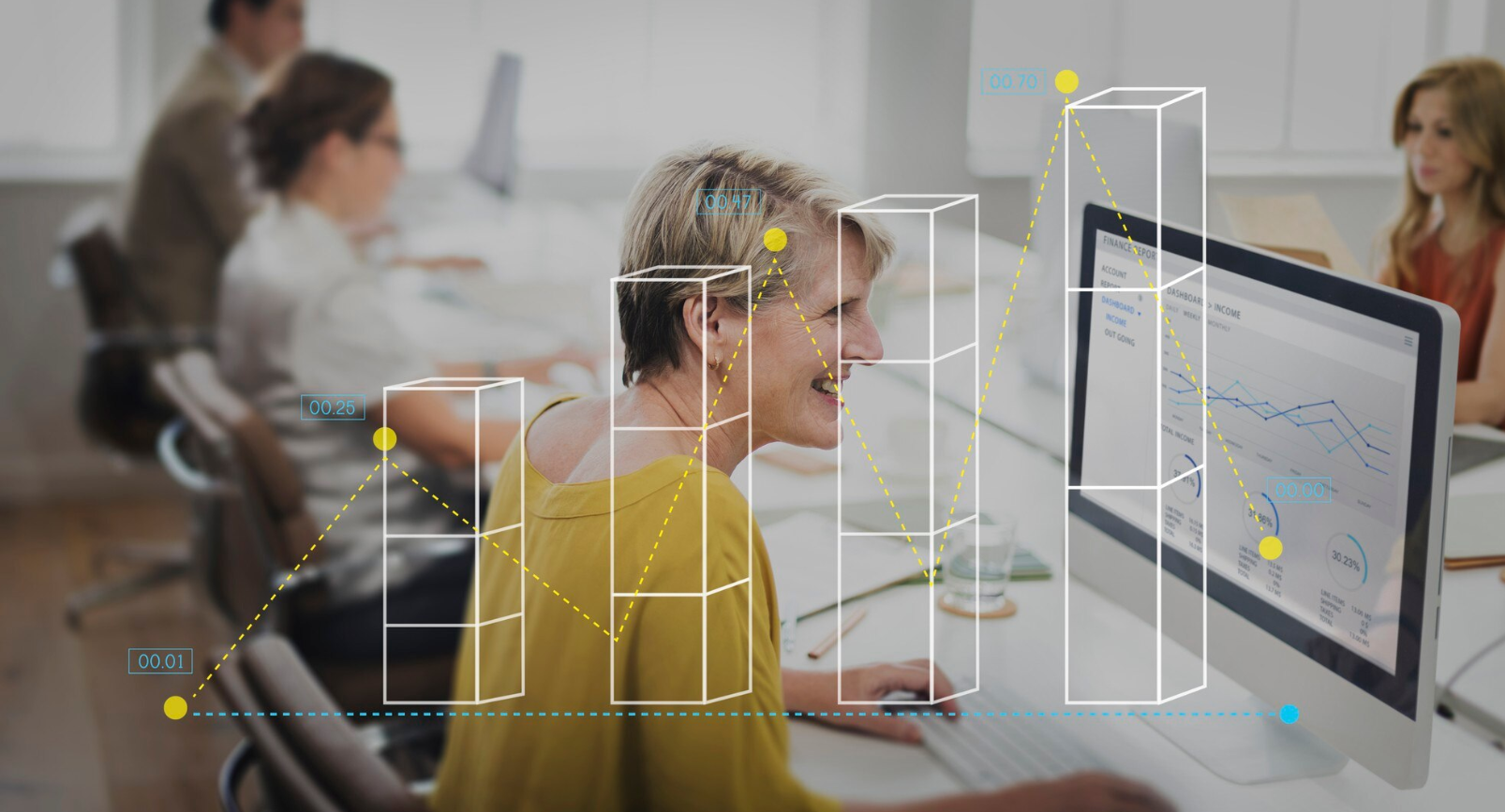
3.Safety and Compliance
Businesses must establish compliant processes covering safety, environmental protection, and quality control. EAM records and tracks regulatory requirements (e.g., safety standards, emissions, quality checks) and auto-generates audit trails. One pharmaceutical company reduced FDA audit prep time from 14 days to 5 days, cutting compliance costs by 65%.
Critically, when integrated with IoT sensors, EAM monitors safety parameters (e.g., pressure, flow) in real time, triggering shutdowns within 10 seconds of anomalies. This allows proactive risk mitigation—preventing injuries, leaks, fires, or accidents. An oil company reported an 80% drop in high-risk operations and zero major safety incidents over five years of EAM use.
Combining “traceable compliance, interruptible risks, and predictable hazards” with precision preventive maintenance, this mechanism elevates production environment reliability, synchronizing safety control with operational efficiency.
4.Strategic Asset Decisions Using EAM
EAM’s robust analytics turn real-time data into actionable insights—enabling proactive maintenance, automated task scheduling, and prioritized asset management.
When managing 50,000 substations, a grid operator relied on manual experience for inspection routes. After EAM optimization, real-time data on equipment age and maintenance cycles reshaped inspection frequency and routes, saving $12 million/year in labor costs. This reveals the system’s deeper value: transforming asset management from an art to a science.
Built-in equipment performance models establish dynamic Overall Equipment Effectiveness (OEE) metrics, pinpointing underperforming assets. Retrofitting or retiring chronically low-efficiency equipment can boost total asset utilization by over 20%. End-to-end data integration—from procurement and installation to operation and decommissioning—extends asset lifespans and maximizes lifecycle value.
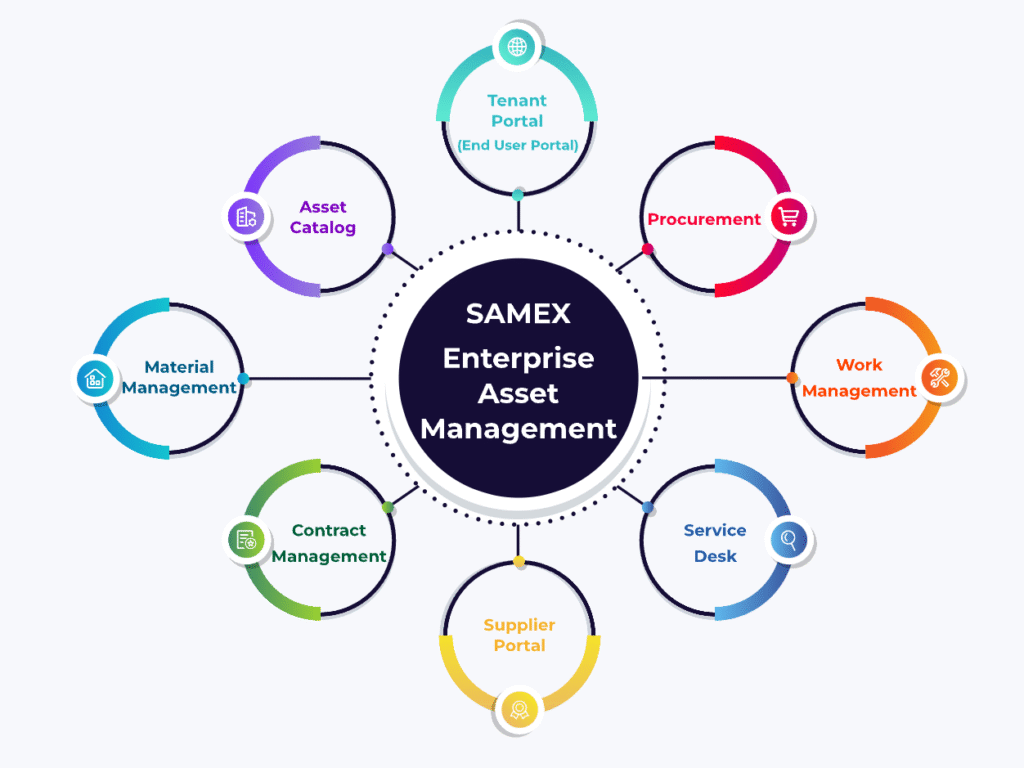
As IoT and AI converge, modern EAM transcends traditional work order management, evolving into a strategic nerve center. In an era where industrial competition shifts from “scale expansion” to “quality and efficiency,” leveraging EAM to reshape the asset value chain has become a benchmark of corporate vitality. This silent management revolution is redefining the core competitiveness of the industrial age. Click to learn more about SAMEX EAM.