1. Definition of Equipment and Facility Management Solutions and Industry Necessity
An Equipment and Facility Management (FM) solution, a specialized form of Facility Management Software, is a systematic management framework established by enterprises to ensure the continuity of production activities and enhance asset performance. It encompasses the entire lifecycle management of equipment, from planning and procurement, through operation and maintenance, to decommissioning and disposal.
In today’s highly mechanized production environment, equipment serves as the foundation of an enterprise’s core productivity. Its operational status directly determines product quality, on-time delivery rates, and safety compliance. Especially within facility-intensive industries, scientific Facility Management Software has evolved from “optional support” to a critical infrastructure for sustainable operations and competitive development.
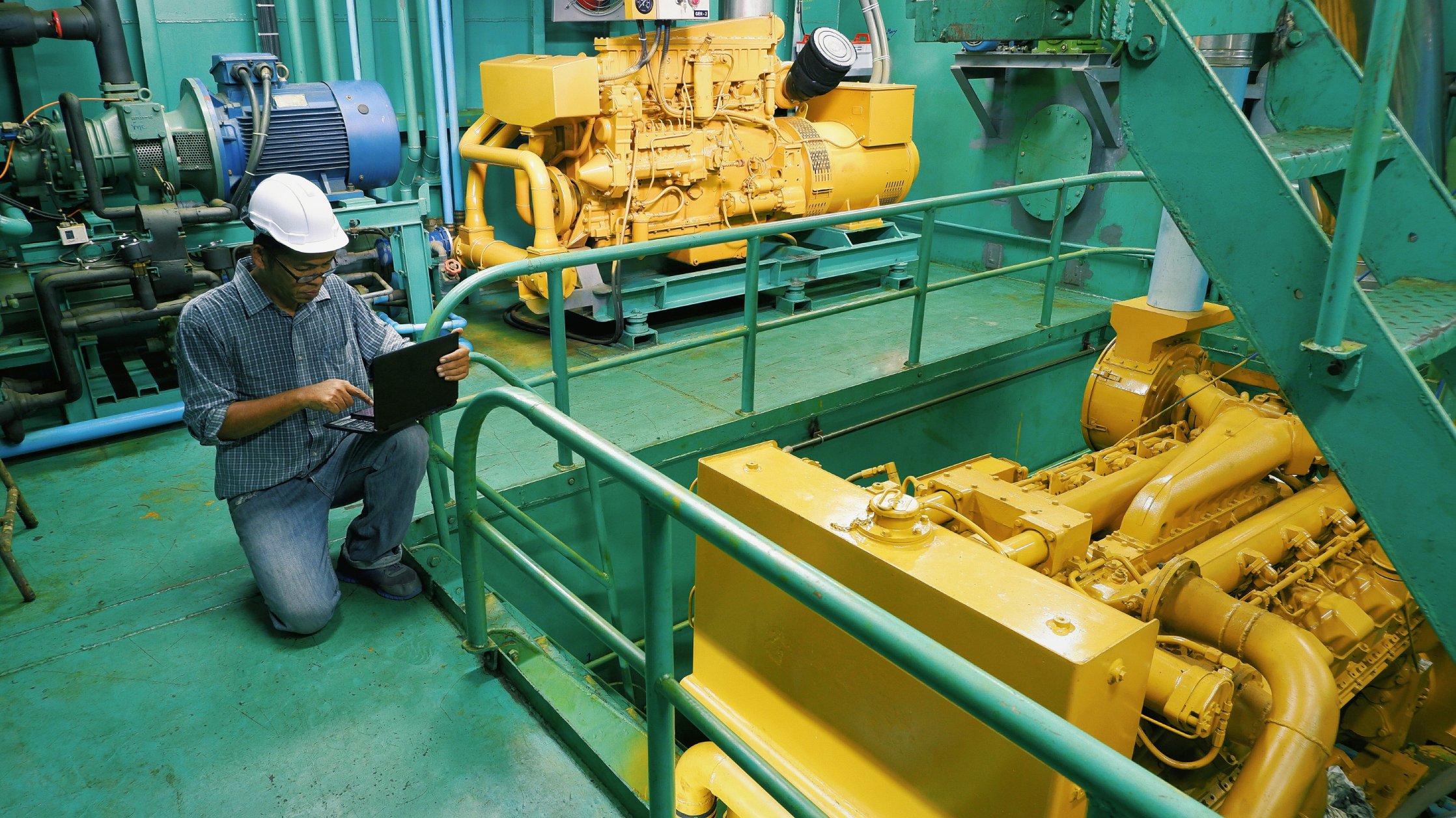
For instance, in the steel manufacturing industry, sudden blast furnace failures can incur hourly production losses exceeding millions of RMB. Proactive Facility Management Software delivers critical protection against such risks. In the semiconductor sector, precision deviations in lithography equipment may scrap entire product batches — a scenario prevented by robust Facility Management Software.
These industries share characteristics such as high equipment value and significant downtime costs. Structured Facility Management Software solutions enable preventative control, shifting from reactive repairs to proactive operations and maintenance (O&M), ensuring stable production systems.
II. Core Value of Implementing Equipment and Facility Management Solutions for Enterprises
1. Achieving Comprehensive Leap in Management Efficiency
Traditional equipment management models heavily rely on manual records and cross-departmental coordination, often suffering from delayed responses due to information gaps. Structured Facility Management Software reconstructs the O&M system through:
- Data Centralization: Dynamically updated digital ledgers integrate equipment parameters and maintenance records, enabling “one source, one file” accessibility.
- Process Automation: Work order engines auto-dispatch tasks with mobile progress tracking, forming digital “initiation-execution-closure” workflows.
This Facility Management Software transformation reduces approval times by 80% and eliminates coordination friction, multiplying information flow efficiency.
2. Extending Equipment Lifespan and Restructuring Cost Models
Unexpected equipment failures act like a “hidden tax” on enterprises, generating not only high repair costs but also continuously eroding profits through production halts, order delays, and resource idleness. Scientific management solutions achieve lifespan extension and cost optimization through a three-pronged mechanism:
- Preventative maintenance plans dynamically adjust maintenance cycles based on equipment operating parameters (such as vibration frequency, temperature curves, energy consumption fluctuations), avoiding both over-maintenance and under-maintenance.
- Comprehensive lifecycle records meticulously detail each repair’s replaced parts, labor hours consumed, and root causes of failure. Big data analysis identifies high-frequency failure points, guiding technical improvements.
- An intelligent spare parts linkage system automatically generates procurement recommendations based on failure predictions, enabling enterprises to reduce inventory costs while simultaneously decreasing downtime due to parts shortages.
This refined management approach extends the average service life of equipment by 3-5 years and reduces capital renewal investments by 20%-30%.
3. Paradigm Shift Driven by IoT and Intelligence
When traditional management methods encounter bottlenecks, next-generation Facility Management Solutions integrating IoT and AI are opening new dimensions. Their core value lies in shifting management actions from “post-incident handling” to “pre-emptive intervention” through a “data sensing – intelligent analysis – autonomous execution” closed loop.
- At the data sensing layer, sensors installed on equipment—such as vibration sensors, infrared thermal imagers, and current detectors—collect operating parameters in real-time.
- At the analysis and decision-making layer, algorithmic models perform deep learning on the data.
- Finally, at the execution layer, the system automatically triggers responses. This intelligent leap upgrades enterprises from a labor-intensive “man-watching-machine” model to a decision-intensive, “data-driven” paradigm.
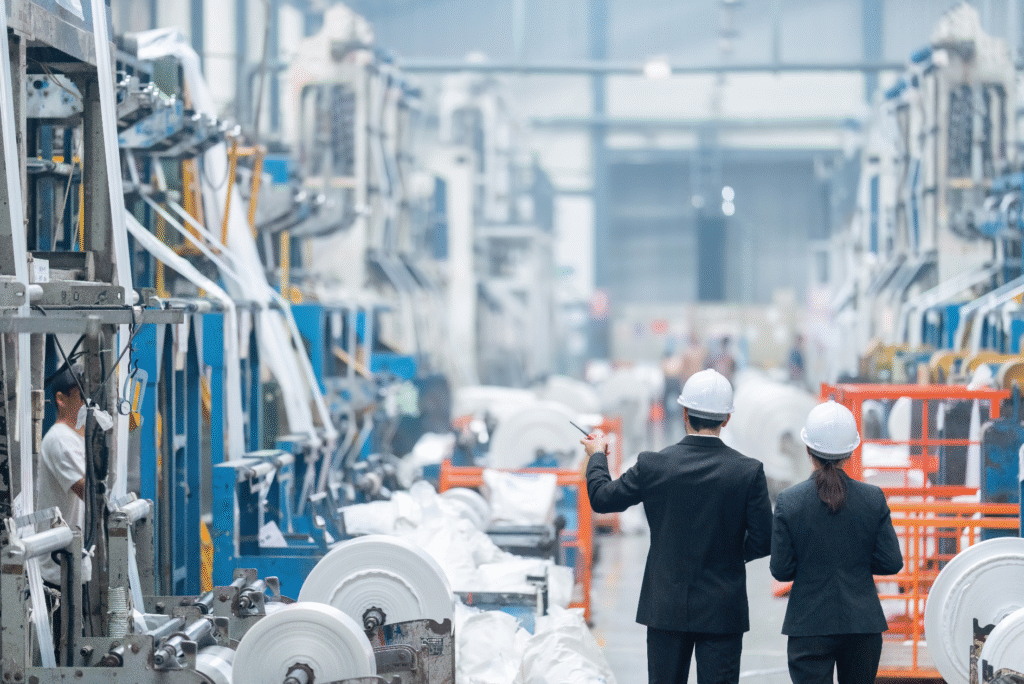
III. Differentiating Advantages of the SAMEX FM Solution
Among numerous equipment management solutions, SAMEX FM wins the favor of facility-intensive enterprises with its unique value proposition, evident in three strategic dimensions:
1. Flexible Customization and Deep Integration Capabilities
Unlike standardized packages, SAMEX FM adopts a modular microservices architecture, allowing flexible assembly like “industrial LEGO.”
Facing the complex environment of multi-protocol equipment coexistence in electronics manufacturing (e.g., Modbus, Profinet, OPC UA coexisting), its edge computing gateway achieves seamless integration for over 97% of devices. When integrating with existing enterprise systems (like SAP, MES), its low-code platform enables rapid API interface development, achieving bidirectional work order data synchronization within two weeks.
This flexibility allows enterprises to independently add monitoring modules for various equipment via the configuration interface during capacity expansion, eliminating the need for secondary development.
2. Industry-Specific Expertise Accumulated Through Deep Cultivation
Since its founding in 2006, SAMEX has consistently focused on the digitalization of enterprise asset and facility management, being one of the first service providers in the Asia-Pacific region to promote EAM/CAFM standardization. Nearly two decades of continuous dedication have resulted in a cross-industry, multi-scenario solution library, with a service network covering Mainland China, Hong Kong, and Southeast Asia.
Currently, the company provides system support to leading clients in sectors such as facility management, manufacturing, commercial real estate, and culture & tourism, including renowned enterprises like Hang Lung Group, Chinachem Group, Gree Electric Appliances, and Chimelong Group.
This long-term focus has yielded not only technological iteration but also profound insights into industry pain points—such as the strong demand for predictive maintenance in manufacturing and stringent safety compliance standards in the culture & tourism sector—which are distilled into rapidly reusable management paradigms.
3. Proven Implementation Results Across Multiple Industries
SAMEX’s solutions have demonstrated value in numerous benchmark projects. Below are key results extracted from selected case studies:
Chimelong Ocean Kingdom (Theme Park):
Deployed an equipment safety compliance engine for real-time monitoring of operational parameters for critical facilities like roller coasters and aquariums. Achieved zero annual safety incidents and improved fault response speed by 50% [Detailed Case].
Gree Electric Appliances (Manufacturing):
Built an IoT predictive network at the Zhuhai production base, conducting vibration monitoring on 200+ injection molding machines. Achieved 48-hour fault warnings, reduced unplanned downtime losses, and increased OEE by 22% [Detailed Case].
Hang Lung Group (Commercial Real Estate):
Implemented group-wide asset digitization and an automated work order system. Reduced O&M costs by 25% and improved equipment inventory efficiency by 90% (compressing a 30-man-day workload to 3 hours) [Detailed Case].
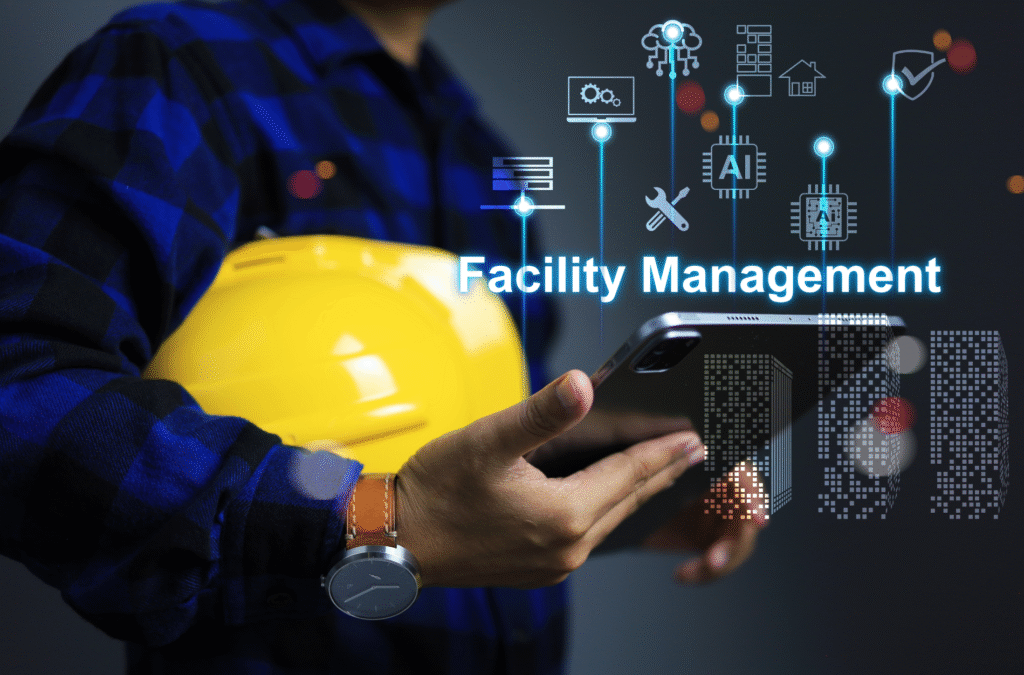
IV. The Strategic Position of Equipment Management Systems in Modern Enterprises
In the era of accelerating Industry 4.0 and smart manufacturing, Equipment and Facility Management Systems (EFMS) have evolved from basic support tools into strategic components of core enterprise competitiveness. They function like the enterprise’s “digital nervous system,” continuously empowering the stability and efficiency of production systems by sensing equipment status in real-time, intelligently coordinating resource allocation, and predicting and mitigating operational risks.
Especially in facility-intensive industries, scientific management systems can transform equipment availability into market responsiveness, convert maintenance cost optimization into profit growth points, and upgrade compliance requirements into safety moats.
As more enterprises embrace digital transformation, organizations that proactively build intelligent equipment management systems are gaining significant first-mover competitive advantages. In the future, with the deep penetration of AI and the Industrial Internet of Things (IIoT), equipment management will evolve into “self-sensing, self-deciding, self-optimizing” intelligent agents. Building such systems is undoubtedly a critical investment for enterprises to secure victory in the era of smart manufacturing.